Composizione della ZAMAK per pressofusione
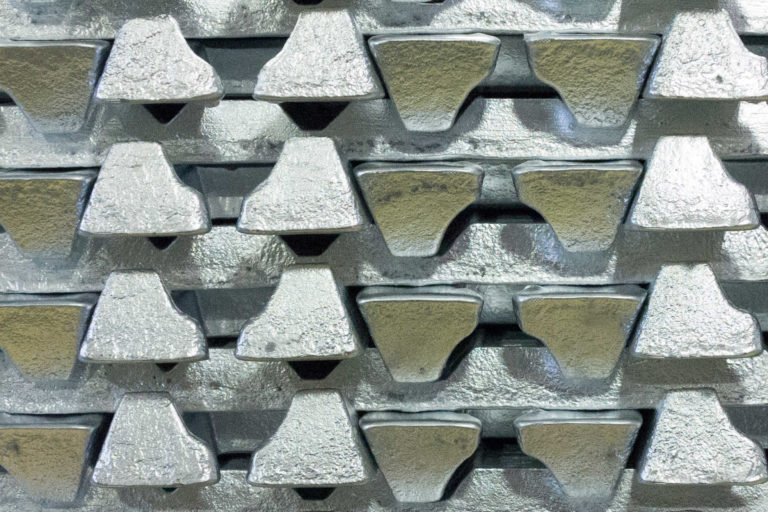
In questo post parleremo della composizione delle diverse leghe di zinco note come Zamak e di come la scelta possa influenzare il risultato della pressofusione in camera calda.
Che cos’è la ZAMAK
Con l’acronimo ZAMAK si intende una tipologia di leghe di zinco brevettata originariamente dalla New Jersey Zinc Co., e composta da quattro metalli principali: zinco, alluminio, magnesio e rame. Questa combinazione di elementi si prestava talmente bene alla lavorazione da divenire in breve tempo sinonimo di lega di zinco per pressofusione in tutto il mondo.
Il vantaggio offerto da questa diffusione è notevole: infatti l’utilizzo di una nomenclatura comune per indentificare la stessa composizione chimica permette ai progettisti di evitare fraintendimenti nella condivisione dei disegni e di reperire facilmente il materiale.
Tra le caratteristiche meccaniche di questa lega, ricordiamo una rigidezza di circa 1,3 volte maggiore a quella dell’alluminio e un carico di rottura pari a circa 2/3 di quello dell’acciaio, oltre a sopportare un carico di snervamento vicino al suo carico massimo. Inoltre, ricordiamo alcune sue caratteristiche fisiche poco note:
- Potere di schermatura elettromagnetica
- Alto fattore di smorzamento delle vibrazioni
- Materiale antiscintillante
Ma perché utilizzare una lega invece del metallo puro?
Per rispondere a questo interrogativo è necessario analizzare le caratteristiche fisiche, meccaniche e microstrutturali di una lega: l’unione di diversi elementi influisce infatti su proprietà fondamentali nell’industria metallurgica, come la resistenza alla corrosione, la conducibilità elettrica, la tenacità e il punto di rottura. Inoltre, utilizzando una lega è possibile abbassare il punto di fusione del metallo, risparmiando così energia destinata al riscaldamento delle fornaci e limitando l’erosione del crogiolo.
Le leghe offrono anche la possibilità di scegliere, entro alcuni limiti, la composizione chimica, la microstruttura più adeguata alla modalità di solidificazione e alle operazioni successive al processo di fusione. La scelta dipenderà anche dal tipo di componente da produrre, tenendo conto delle caratteristiche prestazionali richieste. Tra queste ricordiamo:
- Tenuta a pressione;
- Resistenza alla corrosione;
- Finitura superficiale;
- Accuratezza dimensionale;
- Resistenza all’usura;
Non meno importanti sono però i requisiti della produzione: quando si tratta con metalli da pressofusione in camera calda è necessario tenere conto dei seguenti tre fattori principali.
- Fluidità
Con fluidità si indica quella caratteristica tecnologica di una lega che ne misura la capacità di fluire in uno stampo riempendo spessori sottili. Si definisce caratteristica tecnologica poiché dipende sia dal materiale che dalle caratteristiche del processo, in particolare dalla solidificazione e dallo scambio termico con lo stampo. - Resistenza alla criccatura a caldo
Questo termine indica la capacità di una lega di sopportare sollecitazioni dovute alla contrazione durante il raffreddamento e la solidificazione. - Ritiro da solidificazione
Questa caratteristica influisce sulla possibilità di formazione di porosità e criccature nel pressofuso.
In particolare, per alcuni processi rapidi come la pressocolata in camera calda sono particolarmente indicate leghe resistenti alla criccatura a caldo, mentre si possono utilizzare senza problemi leghe a bassa contabilità.
ZAMAK per pressocolata
Esistono 3 tipi principali di leghe di zinco da pressocolata:
- Leghe al ~4% di Alluminio;
- Leghe al 8-27% Alluminio;
- Leghe proprietarie;
Per ognuno di questi gruppi esistono prodotti con diverse percentuali dei metalli secondari. Le leghe maggiormente indicate per la pressofusione in camera calda sono la Zamak 3, 2, 5 e 8: si tratta di quelle leghe con una percentuale di alluminio variabile dal 2,5% al 28%.
La presenza di alluminio nelle leghe di zinco ha tre motivi principali: per prima cosa riduce il punto di fusione della lega, diminuendo l’apporto di energia termica impiegato dai macchinari, offrendo un risparmio energetico; inoltre riduce anche l’aggressività della lega nei confronti dell’acciaio, materiale di cui sono fatti il sifone, il crogiolo e lo stampo allungando perciò la vita di questi strumenti; infine aumenta la fluidità della lega permettendo di ottenere spessori minori e di facilitare lo stampaggio. Se la lega perde alluminio diminuisce anche la sua colabilità, aumentando il rischio di criccaggio a caldo e di incollamenti nello stampo.
Il rame è il terzo componente per dosaggio nella lega, con quantità che possono variare da 0% a 3,5%. A differenza dell’alluminio che è sempre presente, il quantitativo di rame può essere nullo: questo perché nonostante la presenza di rame aumenti le caratteristiche meccaniche, la durezza e la resistenza all’usura, allo stesso tempo diminuisce l’allungamento percentuale a rottura e la tenacità della lega. Inoltre, può causare instabilità dimensionale: ciò significa che il getto tende ad aumentare di dimensioni col passare del tempo.
Il comportamento del magnesio è simile a quello del rame: esso può costituire un vantaggio o uno svantaggio. A seconda dei casi e delle dosi può essere considerato quindi parte della lega o un’impurità: ad esempio, può essere aggiunto alla lega per contrastare gli effetti della corrosione intergranulare, ma ha un forte impatto negativo sulla colabilità se supera lo 0,05%. Altri effetti legati alla presenza del magnesio sono l’aumento della durezza della lega, un maggiore rischio di criccatura a caldo e altri problemi di finitura superficiale.
A questo punto dovrebbe risultare evidente che anche piccole percentuali di componenti estranei possono avere una grande influenza sui risultati ottenibili tramite pressofusione, e non sempre positivi.
Nella tabella seguente troverete un elenco dei contaminanti e della loro influenza sul pressofuso:
È quindi fondamentale effettuare dei controlli sulla materia prima acquistata, in modo tale da evitare di scoprire a produzione avviata che la formazione di difettosità nei pressofusi dipendeva semplicemente da piccole percentuali di metalli estranei infiltratesi nella materia prima.
Scegliere il tipo di ZAMAK
In generale, possiamo riassumere così i tratti salienti delle leghe più comuni:Le tipologie più utilizzate di zamak nella pressofusione sono la ZP5 e la ZP3. Questo perché si tratta di leghe meno costose rispetto alla ZP8, che viene quindi utilizzata solo per lavorazioni che richiedono resistenza e durezza superiori o maggiore stabilità dimensionale. Anche la ZP2 offre risultati simili in termini di resistenza all’usura e caratteristiche meccaniche, ma risente maggiormente dell’espansione e contrazione dimensionale da invecchiamento.
In generale, possiamo riassumere così i tratti salienti delle leghe più comuni:
Concludendo, la scelta della lega dipende dalle necessità progettuali. Dal momento che anche una minima variazione delle dosi dei componenti ha un grande impatto sul risultato finale, è importante scegliere con cura e affidarsi a fornitori di fiducia.