Vernici, placcature e altri tipi di rivestimenti superficiali
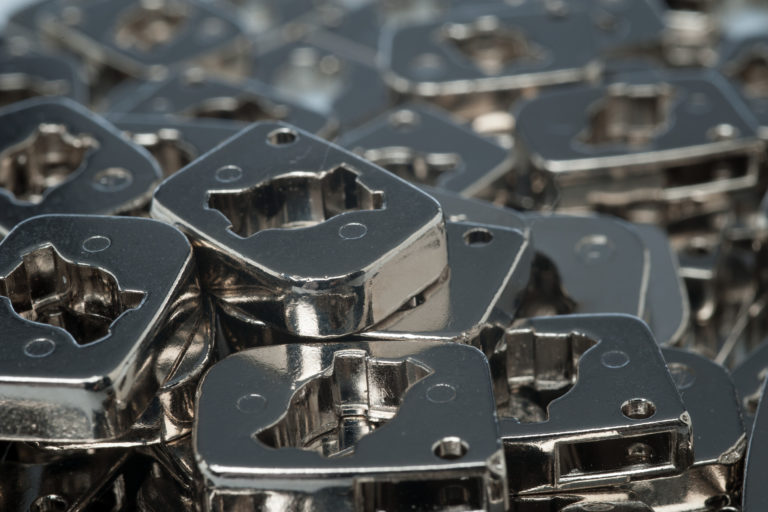
In questo post elencheremo e definiremo i rivestimenti superficiali più comuni per i pressofusi in lega di zinco e i loro effetti. Inoltre, illustreremo tre diversi casi in cui l’applicazione di uno specifico trattamento ha migliorate le performance complessive del componente.
Specifiche tecniche dello zinco
La grande maggioranza dei pressofusi richiede delle lavorazioni specifiche per andare incontro ai requisiti estetici, per migliorare la resistenza all’usura o per ottenere una barriera protettiva contro la corrosione: molte parti hanno bisogno di essere migliorate tramite operazioni secondarie, prima di essere spedite.
Alcuni metalli sono più adatti a subire trattamenti galvanici, verniciature e smaltature di altri: uno di questi metalli è lo zinco. Lo zinco è un metallo denso, molto durevole e più forte rispetto a materiali plastici, come i polimeri. Lo zinco pressofuso permette inoltre di ottenere angoli di sformo più stretti, fori più piccoli e lunghi e pareti più sottili, dando la possibilità di sviluppare forme innovative. Questo, unito alla possibilità di utilizzare dei trattamenti superficiali non-convenzionali, offre dei vantaggi competitivi rispetto alla concorrenza. Scegliendo di lavorare con lo zinco, i designer possono scegliere tra un’ampia gamma di rivestimenti superficiali, in grado di impartire diverse texture e miglioramenti superficiali.
I designer e i project manager sono sempre in cerca di nuovi modi per migliorare i propri prodotti: una collaborazione con un fornitore può aiutarli ad identificare i punti critici nel progetto o a risolvere problemi pre-esistenti. In una collaborazione di co-design, il fornitore può suggerire al cliente il modo migliore di ottimizzare il prodotto per le finiture, basandosi sulla sua esperienza.
La scelta del materiale e del rivestimento
Durante la collaborazione, il primo passo è la scelta della giusta lega e della valutazione delle sue performance tenendo conto dell’uso finale del componente. Il primo punto da chiarire è se il componente deve essere utilizzato all’interno o all’esterno: nel secondo caso, sarebbe consigliabile applicare un trattamento di resistenza alla corrosione. Ci sono diversi tipi di corrosione, che dipendono dal metallo scelto e dall’ambiente circostante.
Un altro criterio di cui tenere conto è la necessità di un trattamento estetico: a seconda dell’utilizzo finale del componente, i clienti potrebbero richiedere una verniciatura, smaltatura, cromatura o placcatura.
Dopo aver analizzato ogni aspetto tecnico, è importante studiare i vantaggi dei diversi tipi di rivestimenti superficiali: tra questi vedremo lo zinco nero, i rivestimenti a conversione chimica-elettrica, i rivestimenti liquidi spray e cotti, placcatura in rame-stagno-zinco, placcatura in rame-nichel-cromo, placcatura meccanica e rivestimenti in polvere epossidica e poliestere.
Zinco Nero
Durante questo processo, uno spesso strato di fosfato nero viene applicato al pressofuso e funge da protezione contro l’umidità e gli ambienti corrosivi. È solitamente un pre-trattamento, in cui la placcatura è seguita da un rivestimento di conversione al cromo nero.
Rivestimenti a conversione chimica-elettrica
Questi rivestimenti superficiali prevedono un immersione chimica che forma una pellicola protettiva sulla superficie dello zinco. Il loro scopo è di proteggere i componenti durante lo stoccaggio e negli ambienti interni. Solitamente i rivestimenti di conversione sono seguiti dall’applicazione di sostanze idrorepellenti o di vernici per potenziare l’effetto.
Rivestimenti liquidi spray e cotti
Questo tipo di rivestimenti include diversi componenti chimici come epossidici, poliesteri, fenolici e uretani.
Placcatura in rame-stagno-zinco
Il risultato di questa lavorazione è un finish opaco e argenteo sulla superficie dello zinco. Fornisce un’ottima protezione, ma il rivestimento tende ad ossidarsi col tempo, diventando nero.
Placcatura in rame-nichel-cromo
Questo trattamento è uno dei migliori per resistere alla corrosione. Protegge la superficie dello zinco contro l’acidità dei bagni successivi, e permette di uniformare la superficie garantendo allo stesso tempo una buona conduttività elettrica.
Placcatura meccanica
Questa procedura prevede il posizionamento delle parti in un tamburo, insieme ad una mistura di polveri metalliche e un attivatore chimico, seguiti dalla burattatura dei componenti fino a che il rivestimento raggiunge lo spessore desiderato. Il rivestimento si forma quindi grazie ad un’azione meccanica e chimica combinata. Il vantaggio di questa lavorazione è che può essere applicata a tutte le superfici, anche negli angoli interni. La colorazione finale dipende dalle diverse combinazioni dei metalli.
Rivestimenti in polvere epossidica e poliestere
Questi rivestimenti superficiali vengono applicati come polveri tramite un processo elettrostatico asciutto, e successivamente vengono fusi in un forno. Il fatto di non utilizzare solventi fornisce un grosso vantaggio, poiché previene la formazione di alcuni difetti legati al loro utilizzo.
Questa non è una lista completa di tutti i possibili trattamenti di finitura, ma è solo una selezione dei più comuni nell’ambito della pressofusione dello zinco.
Ora presenteremo una raccolta di casistiche in cui queste tecnologie sono state implementate e modificate su misura per le richieste del cliente, tramite una collaborazione tra cliente e fornitore.
CASI REALI
L’uso della ZAMAK nei processi di pressofusione rende i componenti adatti a ricevere una serie di finiture diverse, che sarebbero impossibili da ottenere con altre leghe, portando ad ottenere prodotti che hanno sia alti livelli di funzionalità che notevoli caratteristiche estetiche.
Bruschi ha 70 anni di esperienza con i clienti di diverse industrie, che includono l’automotive, l’illuminotecnica, piccoli elettrodomestici per la casa, chiusure per porte e finestre. Grazie a queste conoscenze trasversali, i nostri designer possono offrire soluzioni alternative, provenienti da altre industrie e che garantiscono sempre il massimo della qualità nel materiale, nei procedimenti, nella produzione e nella durata dei prodotti.
CASO 1 – Un nuovo rivestimento per evitare le bolle
Un cliente importante nel settore dell’automotive aveva chiesto a Bruschi di ricreare un componente che veniva in precedenza prodotto da un diverso fornitore. Il cliente voleva una nuova soluzione poiché il prodotto aveva una percentuale di scarto superiore al 25% a causa delle bolle che si formavano dopo il trattamento galvanico.
Bruschi ha lavorato concentrando i suoi sforzi, anche tramite la sua rete di fornitori, per evitare la formazione delle bolle. La soluzione è stata cambiare il rivestimento: passando da un rivestimento galvanico alla passivazione, la percentuale di scarti causate dalle bolle è calata dal 25% a poche parti per milione.
CASO 2 – Migliorare la resistenza allo spray salino
Un importante cliente del settore automotive ha chiesto a Bruschi una soluzione per migliorare la resistenza al test dello spray salino di un componente pre-esistente. Questo componente era prodotto da Bruschi ed era destinato ad essere assemblato su automobili subcompatte. Per un nuovo progetto, il componente avrebbe dovuto ricevere un trattamento migliore per soddisfare i requisiti necessari ad essere utilizzato su macchine di lusso. Generalmente, la resistenza allo spray salino è data dall’uso di particolari trattamenti.
Per il componente destinato alle subcompatte, la resistenza garantita era di 120 ore, grazie ad un trattamento chiamato Fe/Zn: tuttavia, questo trattamento non era adatto alle auto di lusso. Per raggiungere il nuovo obiettivo, Bruschi doveva aumentare la resistenza a oltre 1000 ore.
Grazie all’esperienza di Bruschi e alla sua rete di fornitori, il cliente ha raggiunto il suo obiettivo, implementando un trattamento galvanico speciale, che garantiva la resistenza SST di oltre 1000 ore.
CASO 3 – Vernici speciali invece del trattamento al cromo opaco
Per un importante cliente del settore delle serrature, Bruschi ha sviluppato una lavorazione diversa in modo da diminuire la percentuale di scarto. In particolare, il cliente richiedeva un trattamento superficiale al cromo opaco per alcuni suoi componenti, ma a causa della loro geometria complessa e ricca di angoli, era impossibile garantire la qualità richiesta e il tasso di scarti era fuori controllo.
Collaborando con la sua rete di fornitori, in particolare il verniciatore e la compagnia chimica, Bruschi ha sviluppato una vernice speciale per assicurare le stesse caratteristiche ai componenti senza utilizzare il trattamento al cromo opaco. Cambiando la tecnica utilizzata, il cliente aveva gli stessi componenti, ma un tasso di scarti minore.
Questi case study confermano l’importanza dei rivestimenti superficiali e di come una collaborazione con i propri fornitori possa aiutare a ridurre la percentuale di scarto, trovando soluzioni alternative o creando finiture superficiali su misura per ottenere le migliori performance possibili da un componente.
Se vuoi saperne di più sui processi di finitura, puoi leggere altri articoli sull’argomento:
1- Focus sui trattamenti superficiali
2- Tecniche di lavorazione per la finitura dei metalli