Spessori sottili nella pressofusione di zinco: un vantaggio competitivo
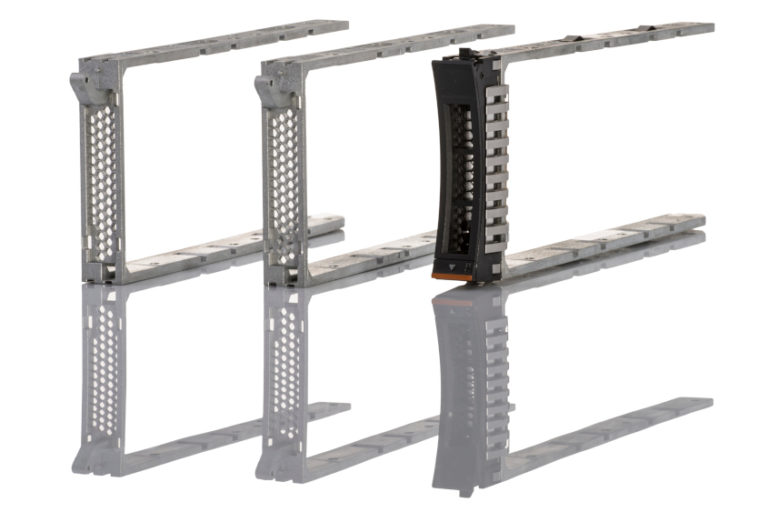
Per alcune tipologie di prodotti è possibile raggiungere spessori sottili nella pressofusione di leghe di zinco. La capacità di ottenere spessori sottili rappresenta un grande valore aggiunto poiché permette di produrre componenti aventi dimensioni e peso ridotti, beneficiando di un risparmio di costi e di materia prima utilizzata.
Spessore minimo ottenibile
La caratteristica delle leghe di zinco che consente di ottenere spessori particolarmente sottili è la proprietà di scorrimento. Grazie a questa proprietà, utilizzando le leghe di zinco, è possibile raggiungere uno spessore minimo di media di 0,4 mm: un valore estremamente basso se comparato con il relativo spessore minimo ottenibile dell’alluminio, come riportato nella tabella sottostante:
Proprietà | Unità di misura | ZP3 | ZP5 | ZP2 | ZP8 | LM24 | A380 |
---|---|---|---|---|---|---|---|
Spessore minimo ottenibile | mm | 0,4 | 0,4 | 0,4 | 0,4 | 1,3 | 1,3 |
Il valore degli spessori sottili ottenibili con le leghe di zinco tramite il processo di pressofusione è determinato da diversi fattori, quali la geometria dell’oggetto e la sua estensione superficiale. Un ulteriore fattore che influisce sul valore dello spessore sottile è la distanza tra lo spessore sottile e il punto di iniezione: minore è la distanza tra lo spessore e il punto di iniezione, minore è il valore di spessore sottile ottenibile.
Grazie alla proprietà di scorrimento e alla possibilità di raggiungere un alto grado di precisione, le leghe di zinco consentono di produrre componenti che non necessitano di ulteriori lavorazioni meccaniche a seguito del processo di pressofusione, poiché già da grezzi sono caratterizzati da finiture precise e, appunto, spessori sottili.
I vantaggi degli spessori sottili
Perché, dunque, la capacità di ottenere spessori sottili costituisce un valore aggiunto nella produzione di un pressofuso?
Di seguito sono riportati i principali vantaggi che scaturiscono dal raggiungimento di spessori sottili, sia relativamente alle caratteristiche del prodotto che in termini di risparmio di costi ed energia:
1. Riduzione di peso dell’oggetto
2. Riduzione di dimensione dell’oggetto
3. Capacità di ottenere prodotti con un elevato grado di dettaglio
4. Resistenza
5. Risparmio energetico
6. Cost saving
1. Riduzione di peso dell’oggetto
La riduzione di peso del prodotto, a parità di funzionalità, è uno dei principali benefici apportati dal raggiungimento di spessori sottili in pressofusi in leghe di zinco. In alcuni settori, ad esempio nell’industria automotive, avere la possibilità di ridurre il peso di un prodotto e di preservarne allo stesso tempo la funzionalità consente di ottenere vantaggi in termini di efficienza; questo è particolarmente vero nel caso di specifici componenti, come ad esempio maniglie e tettucci apribili.
Grazie alla libertà di design offerta dalle leghe di zinco il produttore di pressofusi può, partendo dal disegno originale, studiare e analizzare la geometria del prodotto e collaborare con il cliente per la definizione delle sezioni che possono subire una riduzione di spessore senza intaccare, ma anzi aumentando, la funzionalità del componente. La cooperazione tra cliente e fornitore, un servizio definito co-design, può così portare allo sviluppo di soluzioni innovative che incrementino le performance del prodotto ottenendo, al contempo, una riduzione di costi data dall’inferiore quantità di materia prima impiegata.
La percentuale di riduzione di peso di un componente è ovviamente variabile, poiché dipende dalle caratteristiche di ogni singolo prodotto. Partendo dal progetto originale e arrivando al progetto ridefinito in concerto con il cliente, in alcuni casi è però possibile ottenere una riduzione di peso che arriva fino al 50%: una percentuale di notevole importanza e difficilmente raggiungibile impiegando altri materiali.
Per ulteriori informazioni sulla riduzione di peso dei pressofusi, clicca sul seguente post: Vantaggi del co-design: alleggerimento mirato
2. Riduzione di dimensione dell’oggetto
La riduzione di peso non è l’unica variabile importante per la funzionalità di un prodotto, anche la dimensione assume una grande rilevanza; soprattutto nel caso di quelle apparecchiature cui lo sviluppo tecnologico richiede dimensioni sempre più ridotte.
Attraverso il processo di co-design il fornitore di pressofusi in leghe di zinco studia con il cliente degli interventi volti ad ottenere questa ottimizzazione, individuando le aree della sagoma del prodotto che possono subire una riduzione di spessore.
In particolare, i prodotti con funzione di carter, ad esempio i connettori utilizzati nel settore elettronico, necessitano di spessori sottili per poter essere maggiormente funzionali. Infatti questi prodotti contengono al loro interno altri contenenti ed è quindi necessario, per evitare problematiche di ingombro, che le loro pareti siano il più sottili possibile. Inoltre, per questo tipo di componenti, le leghe di zinco risultano una scelta vincente: non solo, infatti, raggiungono spessori sottili, ma riescono anche a mantenere invariate quelle proprietà di schermatura elettromagnetica che sono estremamente importanti per l’industria elettronica.
Sempre relativamente a prodotti carter, come carter per serramentistica, laddove la funzione meccanica non è primaria, la zama risulta ottimale poiché permette di ottenere spessori sottili con sagome complesse e particolari. Solitamente questa tipologia di prodotto viene realizzata utilizzando come materia prima la lamiera, un materiale altamente elastico che, lavorato con il processo dell’imbutitura, può raggiungere spessori estremamente sottili. Tuttavia la lamiera imbutita, al contrario delle leghe di zinco, non offre libertà di design poiché non consente di ottenere le sagome particolari che possono invece essere realizzate tramite il processo di pressofusione.
Per poter visionare un esempio di prodotto carter che, grazie al co-design, ha raggiunto una riduzione di dimensione e spessori più sottili, con conseguente risparmio per il cliente, puoi guardare questo video.
3. Capacità di ottenere prodotti con un elevato grado di dettaglio
Come anticipato, con il processo di pressofusione dello zinco è possibile ottenere prodotti con un alto grado di precisione e geometrie complesse. Spesso queste geometrie presentano numerosi dettagli di piccole dimensioni, come ad esempio le articolate nervature che caratterizzano prodotti quali connettori e dissipatori.
Nel processo di pressofusione, grazie alla riduzione degli spessori che si riesce ad ottenere, questi dettagli vengono realizzati con estrema accuratezza, garantendo precisione dimensionale e aumentando l’efficienza del prodotto. L’ottenimento di spessori sottili, in questa tipologia di prodotti, è un valore aggiunto anche perché conferisce al componente un elevato grado di elasticità che agevola i sistemi di assemblaggio e di bloccaggio. Test condotti su campioni a spessore sottile in leghe di zinco hanno infatti evidenziato risultati comparabili a quelli delle materie plastiche: in particolare, il modulo di flessione dei campioni in lega di zinco è risultato essere superiore a quello del nylon 6.
4. Resistenza
L’ottenimento di spessori sottili non determina un calo di resistenza del componente: al contrario, un prodotto a spessore sottile in leghe di zinco presenta una microstruttura densa a grana fine che è dotata di proprietà meccaniche superiori rispetto a quella di prodotti con spessori maggiori.
Durante il processo di pressofusione il rapido raffreddamento superficiale genera ciò che viene comunemente definito “pelle di fonderia”, uno strato superficiale di circa 0,2-0,3 mm a struttura fine. I risultati di test su campioni in lega di zinco pressofusa a spessore sottile sottoposti a prove di fatica hanno dimostrato il vantaggio conferito dalla “pelle di fonderia”. Infatti, in un pressofuso a spessori sottili la microstruttura densa a grana fine è percentualmente maggiore rispetto alla massa totale del pezzo, e questo conferisce maggiore resistenza al componente.
Inoltre, ulteriori test su pressofusi a spessore sottile, hanno evidenziato valori di resistenza a fatica notevolmente superiori a quelli riportati in letteratura per leghe di zinco trattare con tecnologie diverse dalla pressofusione.
5. Risparmio energetico
L’ottenimento di spessori sottili e la creazione di componenti dotati di questa caratteristica consentono di ridurre la quantità di energia utilizzata nel processo produttivo. Lo spessore sottile, infatti, implica una riduzione della quantità di materia prima utilizzata e ciò si traduce, in primo luogo, in una minor quantità della materia prima da rifondere.
Inoltre, il componente a spessore sottile ha tempi di raffreddamento ridotti e ciò consente, oltre ad un risparmio energetico relativo al funzionamento delle macchine di produzione, un efficientamento energetico dell’intero processo e una conseguente riduzione dei tempi produttivi.
6. Riduzione dei costi
L’impiego di una minor quantità di materia prima, la maggiore efficienza energetica, la velocizzazione del processo produttivo e la diminuzione di peso e di ingombro, con il conseguente risparmio nei costi di trasporto, sono tutti fattori che consentono una notevole riduzione dei costi di produzione. Il risparmio economico derivato dalla produzione di componenti a spessori sottili si traduce così in un grande vantaggio non solo per il produttore ma anche per il cliente.
La pressofusione di zinco rappresenta quindi una tecnologia competitiva dal punto di vista economico, permette infatti di ottenere spessori sottili ed è la scelta ideale per la produzione di componenti leggeri e resistenti, caratterizzati da sagome complesse e dettagliate.
Per un’overview sui prodotti realizzati in Bruschi, tra i quali figurano prodotti realizzati con la pressofusione di zinco a spessori sottili, clicca qui