Simulazione per pressofusione: conservazione dello stampo e ottimizzazione dei parametri
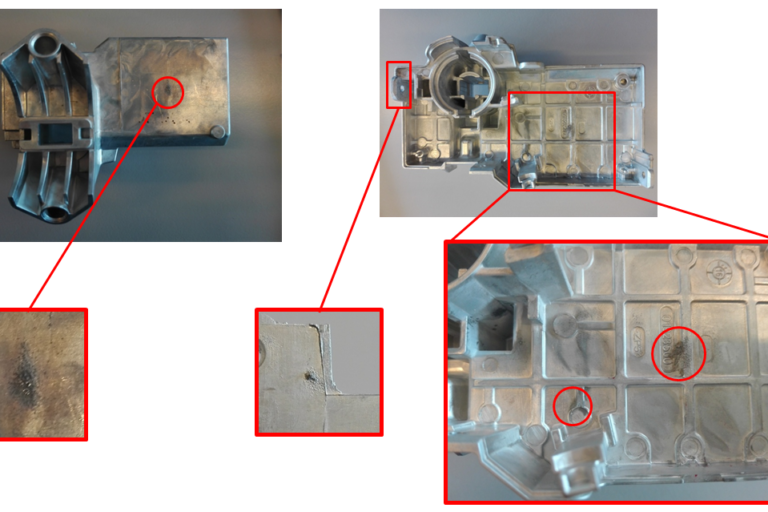
In questo post presenteremo due diversi casi: il primo riguarda la correzione di problemi legati alla conservazione dello stampo di un componente del settore automobilistico, mentre il secondo tratta l’ottimizzazione dei parametri per un componente di piccoli elettrodomestici.
Questo post è l’ultimo di una serie in cui spieghiamo l’importanza della simulazione nella pressofusione in camera calda usando dei casi di studio reali.
Potete trovare una lista completa degli argomenti trattati nel primo post sull’argomento, cliccando qui.
Manutenzione dello stampo: un caso del settore automobilistico
Il prodotto che analizzeremo in questo post è un gruppo di alloggiamento del bloccasterzo per l’industria automobilistica.
La parte più critica è stata la cover superiore dell’alloggiamento, che doveva contenere una carta elettronica. Inizialmente, la parte non era difettata, ma dopo alcune stampate sono comparsi dei chiari segni di erosione dello stampo. L’erosione lasciava infatti dei segni distintivi sulla superficie del componente: queste chiazze scure e irregolari erano un segno dell’usura.
Il deterioramento dello stampo era causato dall’alta velocità del flusso durante le fasi di riempitura e dalla particolare geometria del componente. Le conseguenze di una scarsa conservazione dello stampo possono essere piuttosto gravi, dato che possono causare malfunzionamenti del componente a causa delle irregolarità superficiali, oltre ad aumentare la necessità di riparazioni. Per risolvere il problema, si è ricorso ad una simulazione del processo di riempimento.
Obiettivo e fasi della simulazione
L’obiettivo della simulazione era di trovare opportunità di rallentamento del flusso o di eliminare l’erosione dallo stampo pre-esistente: per ottenere il risultato atteso, il nostro dipartimento di engineering ha svolto un’analisi di sistemi di alimentazione alternativi.
Il primo passo è stato identificare la causa dell’erosione: l’erosione era causata dalla formazione e dall’implosione non-stazionaria di bolle di lega contro la superficie dello stampo. A causa delle alte velocità del flusso attraverso canali stretti in prossimità del canale di alimentazione, la pressione crollava al di sotto del livello di vaporizzazione della lega, causandone l’evaporazione immediata.
Conseguentemente, la lega entra nello stampo con una sezione trasversale più ampia dell’attacco di colata, causando un’espansione che riduce la velocità del flusso. La pressione aumenta rapidamente, causando l’implosione delle bolle di vapore e l’erosione della superficie interna dello stampo.
Risultati
Il campo della velocità di riempimento rappresenta la velocità del flusso al momento dell’ingresso nel volume di controllo.
Dal momento che la cavitazione è un processo non-stazionario che avviene nella prima fase del riempimento, che è anche la fase a più alta instabilità, lo studio della velocità di riempimento fornisce le maggiori probabilità di identificare le aree critiche.
Come si vede dall’immagine seguente, la nuova forma influenza positivamente l’espansione del flusso, limitando i gradienti di velocità entro la linea verde.
Parte interna dell’alloggio
L’area con la cavitazione maggiore è nel centro del campo, dove la linea verde demarca la separazione tra due aree di diversa velocità. Esattamente in quest’area, a causa del rallentamento del flusso e dell’aumento della pressione, le bolle di lega implodono e danneggiano lo stampo.
Con il nuovo diffusore la linea verde si è spostata, generando un allargamento nella diffusione del flusso. Questo ampiamento dovrebbe spostare l’area di cavitazione e ridurne il rischio grazie al minor gradiente di velocità nelle aree critiche dello stampo.
Parte esterna dell’alloggio
La linea verde si è spostata anche sul lato fisso dello stampo, aumentando la diffusione e diminuendo il gradiente di velocità trasversale.
Concludendo, l’uso della simulazione ha permesso di identificare le aree critiche in cui si formava la cavitazione e di progettare un flusso più ampio per spostarla, impedendo l’usura dello stampo e migliorando la conservazione dello stampo.
Passiamo ora al prossimo caso, che riguarda i piccoli elettrodomestici casalinghi e l’ottimizzazione dei parametri.
Ottimizzazione dei parametri: un caso nel settore casalinghi
L’oggetto di questo secondo studio è una maniglia cromata. Il prodotto è un componente per una macchinetta del caffè a cialde: in questo caso non c’era un problema da risolvere, ma era necessario individuare il metodo di riempimento più corretto per ottimizzare la produzione.
Per ottenere un alto livello di qualità estetica, lo stampo deve essere mantenuto a temperature molto elevate: le alte temperature infatti riducono il raffreddamento durante la fase di riempimento, riducendo i segni di flusso. Tuttavia, alte temperature implicano un tempo di raffreddamento più lungo: come conseguenza, il tempo ciclo si allunga a causa della solidificazione più lenta. Di conseguenza, è necessario stabilire l’intervallo di temperatura che permette di ottenere un alto livello qualitativo mantenendo il tempo ciclo il più basso possibile, per aumentare la produttività.
Una volta identificati, i parametri di regolazione della fusione possono essere impostati in modo tale da mantenere le temperature dello stampo nell’intervallo. Questi parametri sono la temperatura di ingresso e il tipo di fluido raffreddante.
Obiettivi e fasi della simulazione
L’obiettivo della simulazione è di stimare i cambiamenti nella qualità superficiale e del tempo ciclo al variare delle temperature dello stampo.
La temperatura dello stampo dipende da due fattori: la geometria del circuito di raffreddamento scelto in fase di progettazione e la temperatura e il tipo di fluido di raffreddamento che viene applicato nella fase di produzione.
Nella simulazione, è stata imposta una temperatura dello stampo omogenea in prossimità delle cavità. La qualità superficiale è stata determinata tramite il valore medio della temperatura della lega alla fine della fase di riempimento, mentre il ciclo produttivo è stato derivato dal tempo necessario al componente per solidificare e raffreddarsi fino a 340°C.
Le variazioni delle due quantità sono state calcolate tramite una serie di simulazioni a temperatura variabile.
Risultati
Il grafico seguente mostra chiaramente i risultati della serie di simulazioni. Tecnicamente, questa non è un’analisi di ottimizzazione poiché le due curve in crescita monotona non permettono di trovare un massimo o un minimo assoluto: può essere considerata come una ricerca di compromesso per definire l’intervallo di temperature ideali.
L’intervallo in cui la curva della qualità superficiale aumenta in modo significativo è tra i 180-228°C, mentre il tempo ciclo del prodotto si mantiene relativamente costante prima di aumentare esponenzialmente.
Per questo motivo abbiamo scelto di mantenere un margine di circa 10°C, all’estrema destra dell’intervallo (218°C < T < 228°C).
In questo caso, la simulazione del componente ha aiutato a determinare la temperatura ideale dello stampo per ottenere la qualità superficiale richiesta, definendo la scelta della temperatura in ingresso e la scelta del fluido di raffreddamento.
Attraverso questa serie di post abbiamo visto diverse applicazioni della simulazione per pressofusione: riduzione di scarti, ottimizzazione delle qualità estetistiche, miglioramento delle caratteristiche meccaniche, conservazione dello stampo migliorata e ottimizzazione dei parametri sono solo alcuni dei molti vantaggi offerti dall’uso di questa tecnologia.