Ottimizzazione del processo di pressofusione: sistema di alimentazione
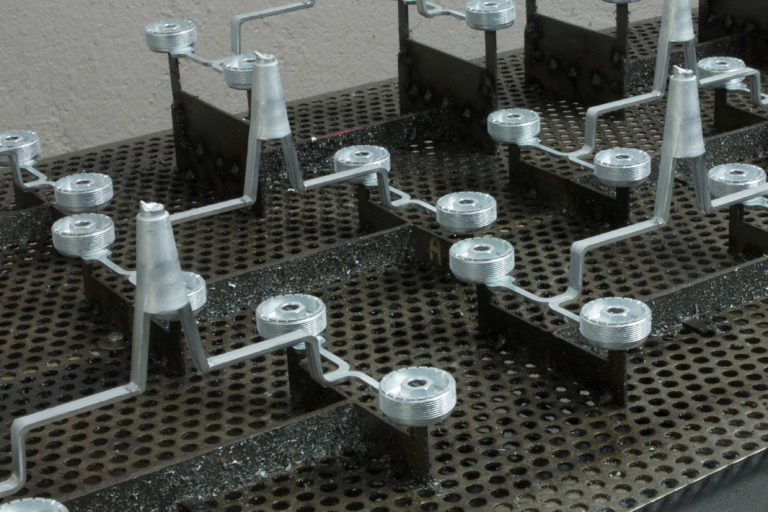
In questo post descriveremo alcune tecniche di progettazione del sistema di alimentazione in camera calda utili per l’ ottimizzazione del processo di pressofusione.
Il sistema di collegamento tra pistone e attacco di colata si compone di due elementi principali: il diffusore ed il canale di colata. La loro struttura e dimensione ha un impatto fondamentale sulla modalità di riempimento, poiché forme diverse possono garantire risultati differenti oltre a permettere di ridurre il rischio di difettosità nel pressofuso.
Posizione dei canali di colata
Per definire la posizione ideale dell’attacco di colata è necessario tenere conto del fatto che il metallo liquido deve percorrere una distanza il più breve possibile in modo da ridurre il rischio di raffreddamento precoce. Per questo motivo solitamente si cerca di dirigere il flusso seguendo la direzione del lato minore della cavità o di sfruttare la presenza di nervature e aperture per facilitare il riempimento dello stampo. In caso di molteplici attacchi di colata, è importante che la direzione dei flussi non sia convergente, poiché in quel caso si avrebbe una perdita di energia e la formazione di turbolenze e bolle d’aria: è quindi buona norma posizionare i canali di colata in modo da ottenere flussi paralleli o divergenti.
La posizione dei canali di colata è inoltre fondamentale per controllare la distribuzione della porosità da ritiro: per ottenere una porosità dispersa e omogenea l’attacco dovrà essere posizionato in corrispondenza delle parti più fini del getto, mentre per ottenere una riduzione della porosità in una zona massiva, l’attacco dovrà essere posizionato in prossimità dello spessore più elevato del pressofuso.
Inoltre, il flusso deve essere diretto verso quelle zone che hanno i maggiori requisiti dal punto di vista qualitativo: in particolare, per ottenere una buona qualità superficiale il flusso deve essere il più diretto possibile. Questi accorgimenti portano ad un maggiore controllo di fenomeni come la porosità da ritiro, permettendo l’ottimizzazione del processo di pressofusione.
Disegno e dimensione dei canali di colata
Un altro elemento importante da considerare per l’ottimizzazione del processo di pressofusione è la forma dei canali di colata. Solitamente la forma più utilizzata è quella trapezoidale, ma per alcune leghe con alta tolleranza, come ad esempio la Zama, si possono utilizzare anche canali a sezione circolare: questa forma permette una minore dissipazione energetica del flusso, mantenendone quindi anche il calore.
Tra i punti di criticità nella progettazione dei canali di canali di colata ci sono la presenza di spigoli vivi e discontinuità nelle deviazioni di flusso, che andrebbero evitati per impedire la formazione di turbolenze. Se si lavora con matrici composte è importante anche prestare attenzione ad errori di costruzione e montaggio, poiché si rischia di creare strozzamenti e scalini che comprometterebbero il passaggio del flusso. Questo tipo di errore può essere risolto in attrezzeria, permettendo un ripristino della funzionalità originale dello stampo.
Durante la progettazione bisogna tenere a mente il rapporto tra la sezione del canale e l’attacco di colata, ma non esiste una regola universale: la scelta dipende dal risultato che si vuole ottenere. Canali più piccoli permettono un risparmio energetico e di materiale, ma richiedono una maggiore potenza del sistema di iniezione e sono maggiormente soggetti a solidificazione precoce. I canali più grandi invece richiedono più materiale ed energia, ma hanno una maggiore efficienza idraulica e portano un maggior apporto termico allo stampo. Di conseguenza, richiedono un tempo di solidificazione maggiore che potrebbe impattare negativamente sui tempi ciclo. La scelta della dimensione dei canali avrà quindi un grande impatto sulla produzione, ed è un passo importante nell’ottimizzazione del processo di pressofusione.
Le sezioni dei canali dovranno inoltre essere decrescenti attraverso tutta la loro lunghezza, e questo vale anche in caso di biforcazioni: la sezione in entrata deve essere uguale o maggiore a quella in uscita. In caso di biforcazioni che portino il metallo a due attacchi di colata uguali tra loro in sezione, anche i rami uscenti dovranno essere uguali tra loro, con una somma minore o uguale al ramo di entrata.
Inoltre, è importante che il volume dei canali permetta che il materiale arrivi contemporaneamente a tutti gli attacchi di colata, ed è per questo che anche la loro lunghezza deve essere costante.
Per permettere al flusso di essere distribuito equamente in tutte le cavità, è necessario collegare il canale di colata all’attacco tramite l’uso di un diffusore.
Il diffusore
Il diffusore è quel raccordo necessario per passare dalla sezione quadra del canale di colata a quella sottile dell’attacco di colata. Esistono diversi tipi di diffusore ed ognuno ha vantaggi diversi, ma le funzioni principali rimangono due: rendere il passaggio tra canale e attacco più graduale, in modo da contrastare la tendenza del metallo a staccarsi dalle pareti, e indirizzare il flusso del metallo. Entrambe le funzioni sono fondamentali per l’ottimizzazione del processo di pressofusione, poiché, a seconda del modello di diffusore scelto, i risultati ottenuti possono essere molto differenti.
I modelli di diffusori più utilizzati sono quello a ventaglio e quello tangenziale:
- Il diffusore a ventaglio produce un flusso stretto con velocità maggiore al centro. Per questo motivo si adatta meglio ad attacchi corti e spessi, è ideale per angoli di apertura ridotti;
- Il diffusore tangenziale produce un flusso più allargato, con velocità maggiore agli estremi. Per questo è più adatto ad attacchi lunghi e sottili e permette di ottenere angoli di apertura elevati;
Indipendentemente dal modello di diffusore scelto, l’andamento della sezione deve decrescere linearmente dal canale verso l’attacco. Questo significa che non basta utilizzare un diffusore trapezoidale, ma sarà necessaria una curvatura della superficie della base o, in alternativa, dei fianchi.
Vantaggi e svantaggi del diffusore diritto
Con diffusore diritto si intende un diffusore con base trapezoidale diritta e fianchi curvi. Il principale vantaggio di questo tipo di diffusore è che l’angolo di apertura è pari alla semi apertura del diffusore, rendendo facile la smaterozzatura, mentre il principale svantaggio è la tendenza a far lavorare l’attacco a freddo. Inoltre nel riempimento effettuato utilizzando questo tipo di diffusore il fronte di avanzamento è più stretto e il metallo tende a staccarsi dalle pareti.
Vantaggi e svantaggi del diffusore curvo
Il diffusore curvo è un diffusore con fianchi diritti e base curva. È ideale in quei casi in cui è necessario alimentare maggiormente i lati, ma l’angolo di apertura è difficile da calcolare. Inoltre porta alla formazione di piccole parti che richiedono un intervento di smaterozzatura. Il flusso generato da questo tipo di diffusore ha una velocità maggiore nel centro dell’attacco ed il metallo tende ad aderire alle pareti.
Anche in questo caso il tipo di diffusore scelto dipende dal risultato che si desidera ottenere, dalla potenza dei macchinari di iniezione e da altre condizioni di contorno. Permettendo un migliore controllo del flusso del metallo e riducendo il rischio di formazione di intrappolamenti di aria, il diffusore è uno strumento fondamentale per l’ottimizzazione del processo di pressofusione.