Come migliorare il processo produttivo per l’industria della pressofusione
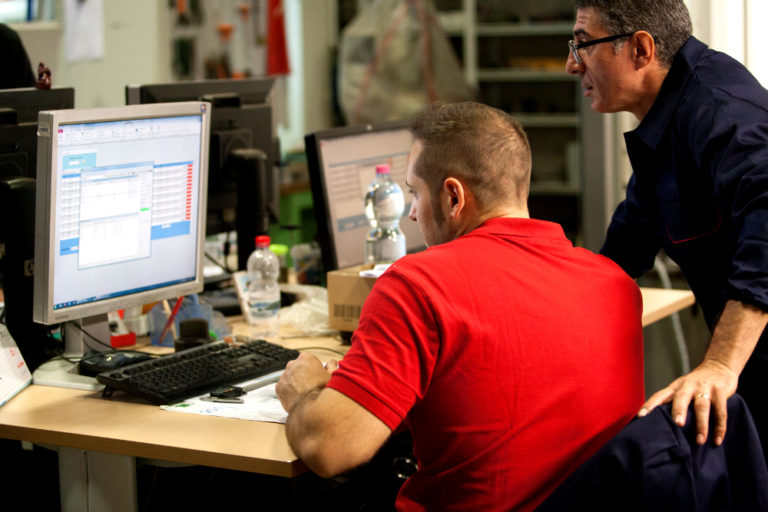
L’ottimizzazione del processo produttivo nell’industria della pressofusione, così come in numerosi altri settori manifatturieri, è un concetto che si riferisce a una serie di azioni intraprese al fine di migliorare i tempi di produzione, ridurre i costi e, di conseguenza, ottenere risultati che soddisfino le richieste del cliente in termini di tempistiche e performance. Il miglioramento della produttività, infatti, rappresenta un vantaggio sia per il fornitore che per il cliente: da un lato il fornitore beneficia di costi ridotti, mentre dall’altro il cliente si affida a un partner che offre prestazioni della qualità richiesta in tempi brevi. La Bruschi ha da sempre considerato questo tema un aspetto centrale per il proprio business, infatti negli anni ha introdotto molteplici misure di controllo e correzione allo scopo di raggiungere un miglioramento del processo produttivo in continua crescita.
Come ottimizzare il processo produttivo
Il potenziamento del processo produttivo può essere sviluppato attraverso un piano d’azione ben definito, che tenga in considerazione la complessità di elementi che caratterizza il dipartimento di produzione. La produzione è infatti composta non solo da macchinari, ma anche da design di prodotto, tecnologie, operatori e attività di pianificazione, per citare alcuni dei componenti più importanti di questo articolato sistema. Per ottimizzare il processo produttivo risulta quindi necessario assumere una visione d’insieme di tutti questi elementi e delle loro variabili, allo scopo di implementare una strategia che sia funzionale su molteplici aspetti.
Di conseguenza, il primo step da compiere è la definizione degli strumenti e delle azioni di modifica che possono contribuire al miglioramento delle diverse fasi della produzione. In Bruschi il piano di potenziamento del processo produttivo è costituito da quattro elementi centrali:
- Automazione
- Simulazione
- Riduzione degli scarti
- Tempo ciclo
-
Automazione
L’introduzione in un sistema produttivo di macchine automatizzate dotate di tecnologie altamente innovative apporta rilevanti benefici in termini di lead time ridotto, abbattimento dei costi e conseguimento degli standard di qualità richiesti dai clienti. La sostituzione di lavorazioni manuali con sistemi automatizzati permette, infatti, di ottenere una maggiore velocità di processo, ottimizzando di conseguenza l’intero lead time. Inoltre, l’automazione comporta una probabilità di errore ridotta rispetto alla lavorazione di un pezzo da parte dell’operatore.
Questo si traduce in una significativa riduzione dei costi di produzione, che è ulteriormente incrementata grazie al risparmio di energia e materiali che l’automazione apporta. L’inserimento di macchine automatizzate nel dipartimento di produzione genera anche un ulteriore vantaggio, che permette di ottimizzare anche il controllo qualità. Infatti, gli operatori che precedentemente eseguivano operazioni manuali sul componente possono, grazie all’automazione, occuparsi di altre attività aventi un maggior valore aggiunto, come il controllo qualità.
Un progetto di ottimizzazione del processo produttivo di un particolare componente, prodotta per un cliente del settore dei piccoli elettrodomestici, ha ottenuto eccellenti risultati in termini di aumento della produttività e riduzione delle attività manuali svolte dagli operatori. Il progetto di ottimizzazione è stato sviluppato per risolvere una situazione di disallineamento di capacità produttiva e richieste del cliente. Attraverso l’introduzione di sistemi automatizzati è stato possibile ridurre questo gap, ottenendo un tempo ciclo ottimizzato. Queste modifiche al processo produttivo hanno apportato benefici significativi: l’aumento del 33% della capacità produttiva e la riduzione delle attività manuali svolte dagli operatori per una percentuale superiore al -95%.
-
Simulazione
La simulazione del processo di pressofusione rappresenta un altro elemento che può contribuire al raggiungimento di un processo produttivo più efficace: grazie infatti all’utilizzo di software di simulazione gli ingegneri possono prevedere le reazioni del materiale all’interno dello stampo. Questo processo è possibile grazie ad un’analisi termo-fluidodinamica dello stampo, nota come CFD simulation (Computational Fluid Dynamics), che permette di localizzare preventivamente potenziali difetti, come porosità, giunzioni fredde e presenza d’aria nel pressofuso.
La fase di simulazione si dimostra quindi particolarmente utile per ottenere una geometria dello stampo ottimizzata prima di iniziare con il processo di produzione. Durante questa fase è infatti possibile selezionare i migliori parametri da applicare per la forma dello stampo, in modo da evitare anticipatamente difetti sul pezzo e di conseguenza ridurre i costi di produzione e lavorazioni meccaniche aggiuntive.
Se desideri informazioni più dettagliate sulla simulazione, ecco altri post sull’argomento:
- I vantaggi della simulazione HPDC nella pressofusione
- Simulazione per pressofusione: qualità superficiale nel settore automobilistico
- Simulazione per pressofusione: conservazione dello stampo e ottimizzazione dei parametri
- Simulazione per pressofusione: studio della porosità da ritiro
-
Riduzione degli scarti
Una progressiva riduzione degli scarti di lavorazione può essere ottenuta attraverso un’accurata pianificazione dell’intero processo produttivo. Innanzitutto è necessaria un’analisi del prodotto e del processo che si concentri sulle cause dello scarto. Per identificare queste cause gli ingegneri devono servirsi di software di simulazione per prevedere tutte le fasi della produzione, dal design ai trattamenti di finitura. La simulazione si dimostra nuovamente uno strumento indispensabile per l’ottimizzazione dei processi produttivi di pressofusione di zinco, poiché permette di evitare difetti e di controllare proprietà tecniche prima di iniziare con la produzione del pezzo, generando così una consistente riduzione dei costi e del lead time. Una volta individuate le principali cause dello scarto si procede alla definizione delle possibili soluzioni da applicare, localizzando i passaggi di maggior rilevanza nel processo produttivo e monitorandoli costantemente.
Per ulteriori informazioni sulla riduzione degli scarti clicca sul post qui sotto:
-
Tempo ciclo
L’espressione tempo ciclo definisce il periodo di tempo richiesto per sviluppare la produzione di un componente. Il tempo ciclo rappresenta una variabile centrale nella produzione di un componente perché un tempo ciclo ridotto si traduce in un ridotto lead time, cioè il periodo di tempo necessario per soddisfare la richiesta di un cliente in termini di offerta. Un lead time ottimizzato genera incremento nella soddisfazione del cliente, poiché permette al fornitore di rispettare le deadline e gli standard ricercati dal cliente. Di conseguenza, per garantire un servizio rapido ed efficiente tempo ciclo e lead time devono essere ottimizzati il più possibile. Il tempo ciclo può essere ridotto prestando attenzione a diversi aspetti del processo produttivo, in particolare alla fase di simulazione e ai sistemi tecnologici del dipartimento di produzione. Innanzitutto, come precedentemente illustrato, è importante simulare le fasi di produzione e definire i parametri più adeguati da applicare per il processo di produzione. In questo modo possibili difetti sul pressofuso possono essere evitati sin dall’inizio e, di conseguenza, sarà possibile eliminare ulteriori operazioni meccaniche. Un altro elemento centrale per la riduzione del tempo ciclo è il sistema tecnologico della fonderia, il cui livello di innovazione tecnologica può apportare notevoli riduzioni nei tempi di produzione. Infatti, macchinari automatizzati permettono di ottenere tempi ciclo più rapidi e operazioni più accurate, variabili che risultano discriminanti nel raggiungimento delle performance ricercate dai clienti. Inoltre, controlli periodici dei macchinari aiutano a comprendere come il tempo ciclo può essere ulteriormente migliorato.
Per informazioni dettagliate sul tempo ciclo clicca sul post qui sotto:
Perché ottimizzare il processo produttivo è fondamentale per un business
L’ottimizzazione del processo produttivo è un elemento decisivo nella gestione di un business perché consente di ridurre i costi di produzione e di ottenere un processo produttivo più rapido. Al fine di conseguire questi benefici è quindi necessario introdurre nel proprio sistema di produzione tecnologie automatizzate e software di simulazione, e ottimizzare la riduzione degli scarti e il tempo ciclo. Con la definizione di un preciso piano di ottimizzazione il lead time potrà essere ridotto e di conseguenza si potrà assistere a un incremento della soddisfazione del cliente.