Pressofusione di zinco: uno sguardo verso il futuro
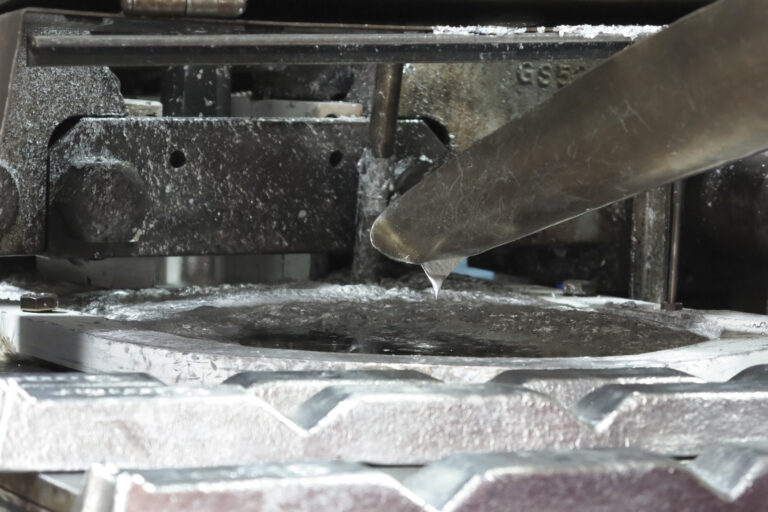
Il processo comunemente chiamato “pressofusione” oppure “pressocolata” consiste nell’iniettare sotto pressione il metallo liquido in uno stampo, generalmente costruito in acciaio speciale, e nel lasciarlo solidificare. Il getto ed il canale di colata (materozza) vengono poi estratti dallo stampo ed il ciclo si ripete. La pressofusione è la strada più breve dal metallo liquido all’oggetto finito e trova impiego in quasi tutti i campi di fabbricazione di manufatti che necessitano di componenti metallici non ferrosi come automobili, elettrodomestici, motori elettrici, radio-televisori, computer.
Il processo di pressofusione si divide in due tipologie principali: pressofusione a camera fredda e pressofusione a camera calda. La differenza consiste nel fatto che nel processo a camera fredda il metallo liquido, nella giusta quantità, viene versato ad ogni ciclo in una camera esterna al crogiolo in cui si trova il metallo fuso, mentre nel processo a camera calda la camera di pressione è immersa nel crogiolo in cui si trova il metallo fuso. In questo articolo parleremo del processo a camera calda, che da oltre settant’anni è il processo praticato dalla Bruschi per la produzione di parti in lega di zinco. I principali vantaggi del processo a camera calda consistono in:
- Rapidità del processo produttivo, a seguito della relativamente bassa temperatura di fusione;
- Maggiore durata degli stampi e delle attrezzature;
- Quasi totale assenza di lavorazioni meccaniche successive.
Gli elementi principali del processo di pressofusione a camera calda sono:
- la pressa, con le relative periferiche (robot, centralina termica, attrezzature per l’eliminazione delle materozze);
- lo stampo.
La pressa e i suoi componenti
La pressa si compone principalmente di due parti: il gruppo iniezione e il gruppo chiusura. Sul gruppo chiusura viene installato lo stampo nel quale sono incise le sagome (cavità) da riempire per ottenere i prodotti pressofusi.
Il gruppo iniezione
Il gruppo iniezione è composto dal forno (1) nel quale è inserito il crogiolo (2), dal sifone (3) e dal cilindro di iniezione (5). Nel crogiolo (2), abitualmente riscaldato elettricamente, si trova il metallo liquido (nel nostro caso, trattandosi di leghe di zinco, a 400°C) nel quale è immersa la camera di pressione (8), da qui la definizione “a camera calda”. La camera di pressione viene riempita per gravità attraverso i fori di rabbocco. Un pistone (4) verticale azionato dal cilindro di iniezione (5) spinge il metallo liquido verso il basso. Il metallo liquido, attraverso un condotto chiamato “collo d’oca” (7), viene così indirizzato verso l’ugello (6) che, essendo in appoggio sullo stampo consente al flusso del metallo di raggiungere le cavità, dette anche impronte, da riempire.
La pressione di circa 30 Mpa (300 bar) applicata sul metallo garantisce il rapido riempimento delle cavità. Infatti il tempo di riempimento delle cavità è uno dei fattori più importanti di cui tenere conto poiché per la buona riuscita del getto è necessario che il metallo non solidifichi fino al completo riempimento della cavità. Si parla infatti di millesimi di secondo e di conseguenza di velocità molto alte nelle zone di ingresso colata, fino a 60 mt/sec.
Il gruppo chiusura
Il gruppo chiusura provvede a tenere serrato lo stampo al momento dell’iniezione tramite un sistema a ginocchiere (4) azionato da un cilindro oleodinamico (2). Si compone di un piano fisso (7) in prossimità del gruppo iniezione e di un piano mobile (5) scorrevole su 4 colonne guida (6). Nella parte posteriore della piastra mobile è fissato il cilindro di estrazione (3) collegato all’elemento mobile dello stampo chiamato “Tavolino di estrazione”.
Lo stampo
Lo stampo si compone di due parti separate del piano di chiusura principale ognuna delle quali contiene parte delle cavità da riempire. La parte fissa (1) ancorata al piano fisso della pressa, e la parte mobile (2), ancorata al piano mobile della pressa. Nelle due metà stampo sono ricavate le cavità (4) da riempire (il negativo del prodotto da ottenere). Nello stampo avviene infatti la fase di raffreddamento e solidificazione. È la fase in cui in pochi secondi il prodotto prende la forma definitiva. Il riempimento avviene attraverso un ingresso sottile circa 0,4 mm che consente di evitare eccessivo testimone sul prodotto. Nel tavolino di estrazione (3) sono fissati i perni estrattori, così chiamati perché, azionati dal cilindro di estrazione, esercitano una spinta sui prodotti solidificati per estrarli dalle cavità dello stampo.
Le apparecchiature periferiche
Al termine della fase di estrazione entrano in gioco le apparecchiature periferiche. L’intero grappolo (o stampata) viene prelevato dal robot (in Bruschi tutte le macchine sono dotate di robot antropomorfi ABB) ed un sistema di fotocellule o telecamere ne controlla la completezza. Il robot deposita poi il grappolo alla fase successiva di eliminazione della materozza e dei canali di colata (alimentazione). Vi sono diverse possibili soluzioni per l’eliminazione delle “materozze”: presse di tranciatura, apparecchiature specifiche per l’utilizzo della movimentazione del robot che simula l’azione umana, o automazioni dedicate.
Pressofusione di zinco: quali prospettive?
La pressofusione moderna è molto diversa da quella di qualche decennio fa. Le attività e le soluzioni che una volta erano affidate alla maestria ed alla abilità dell’operatore sono oggi demandate a sistemi avanzati di controllo del processo gestibili direttamente a bordo macchina ed in remoto. Il progresso tecnologico mette oggi a disposizione macchine dotate di sistemi sofisticati per il controllo dei parametri principali del processo di pressofusione (pressioni, temperature, velocità del metallo e degli azionamenti, tempi di compressione e raffreddamento). L’evoluzione delle macchine di pressofusione va infatti di pari passo con i sistemi avanzati di progettazione. La definizione delle strutture ottimali del prodotto tramite analisi ad elementi finiti porta alla creazione di sagome sempre più complesse e con tolleranze sempre più ristrette che non possono essere realizzate senza l’utilizzo di apparecchiature all’avanguardia.
È perciò indispensabile l’approccio scientifico nella progettazione e pianificazione del processo così come nella soluzione dei problemi produttivi e di qualità sia strutturale sia estetica. Bruschi si è perciò dotata da tempo del programma di simulazione che consente una approfondita analisi di riempimento ed una verifica dei cicli produttivi per la corretta individuazione dei punti di iniezione e l’eliminazione di possibili aree a bassa qualità del pressofuso. Già dagli anni ’80 Bruschi ha costruito e sviluppato il proprio sistema di stampaggio sottovuoto (ad oggi ancora non comune per la pressofusione delle leghe di zinco). Lo stampaggio sotto vuoto consente di ottenere fusioni prive di soffiature per garantire il rispetto dei requisiti sia di resistenza meccanica sia di esigenza estetica.
Le possibilità attuali della pressofusione delle leghe di zinco sono spesso poco conosciute, l’applicazione di adeguate procedure di progettazione e controllo del processo, unite al grado di raffinazione delle leghe, consentono al giorno d’oggi di ottenere risultati inaspettati sia in termini di qualità prodotto che in termini di riduzione dei costi produttivi. Le approfondite analisi delle fasi di solidificazione e raffreddamento danno la possibilità di ottenere un alto grado di precisione nei pezzi ad elevato contenuto tecnico: le attuali conoscenze e possibilità di controllo del processo consentono infatti di ottenere prodotti con precisioni superiori rispetto a quelle abitualmente conosciute e riportate negli attuali standard di riferimento.
Il corretto bilancio termico dello stampo può essere analizzato a fondo con gli strumenti di simulazione e questo dà la possibilità di individuare e correggere le problematiche legate alla produzione di oggetti a spessore molto sottile per ridurre i problemi di peso e di ingombro, ma garantendo la necessaria resistenza del prodotto. Infine, lo studio dei flussi e la conseguente corretta definizione dei canali di alimentazione, nonché dei punti di iniezione e di deflusso, sono indispensabili per il raggiungimento della qualità superficiale necessaria per i prodotti verniciati o trattati galvanicamente. Nella quasi totalità dei prodotti per ogni settore, sia per motivi di protezione, sia per motivi estetici, è previsto un adeguato trattamento superficiale. Pertanto la comprensione delle criticità dei trattamenti superficiali e l’individuazione di adeguate soluzioni si rendono indispensabili per garantire un processo stabile ed affidabile anche nelle fasi a valle della pressofusione.