Focus sui trattamenti superficiali
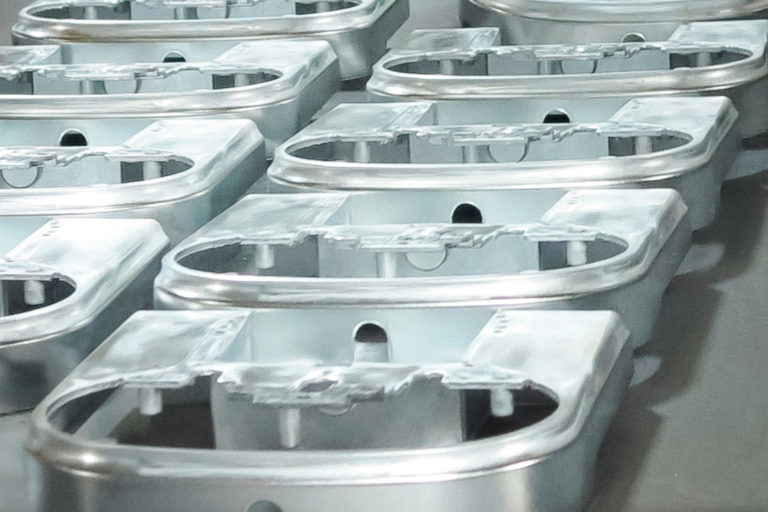
In questo post parleremo dei più comuni trattamenti superficiali e spiegheremo perché è importante prenderli in considerazione già dalla fase di design del componente, offrendo qualche consiglio per l’ottimizzazione dei punti più critici.
Per prima cosa, è importante distinguere tra finiture superficiali e trattamenti superficiali: le prime indicano la texture della superficie, ad esempio se risulta liscia o ruvida al tatto, mentre i secondi identificano tutti quei processi industriali mirati a modificare la texture della superficie.
I trattamenti superficiali includono diversi processi industriali che possono modificare la superficie di un oggetto, prodotto o componente al fine di ottenere o migliorare una sua proprietà o caratteristica. Ad eccezione dei componenti fatti di metallo nobile, quasi tutte le parti in metallo necessitano di un trattamento dopo la produzione. Diversi trattamenti possono essere scelti per diversi motivi: per migliorare l’estetica di un prodotto, per migliorarne la resistenza chimica, la resistenza alla corrosione o all’usura, per migliorarne o modificarne la conduttività elettrica, per rimuovere le bave ed altri difetti o per modificare la texture della sua superficie.
A volte più trattamenti possono essere applicati contemporaneamente, per ragioni estetiche o funzionali: ad esempio, per ottenere un miglior risultato, trattamenti estetici come la cromatura o la verniciatura sono solitamente preceduti da speciali trattamenti preparatori. Ci sono diverse di tecniche di lavorazione: alcune possono essere utilizzate come trattamento conclusivo, mentre altre sono utilizzate per preparare la superficie per lavorazioni secondarie. La scelta del trattamento dipende dal design del prodotto e dalle richieste del cliente. Grazie a questo tipo di lavorazione, è possibile prevenire difetti superficiali causati da agenti esterni che potrebbero danneggiare il componente.
Un altro motivo per applicare un trattamento superficiale è di migliorare la funzionalità del componente: ad esempio, le lavorazioni meccaniche sono utilizzate non solo per limare i bordi taglienti, ma possono anche aumentare la ruvidità per garantire una più facile presa su maniglie e altri componenti simili.
Come abbiamo detto in precedenza, la maggior parte dei prodotti in metallo richiede dei processi di finitura: la maggior parte dei pressofusi di alluminio, magnesio e zinco riceverà almeno un trattamento post-fusione, a seconda delle specifiche di durabilità, protezione ed estetica.
Uno dei processi più comunemente utilizzati nella pressofusione è la sbavatura: le bave sono estremamente comuni e a causa della loro affilatezza costituiscono un pericolo per gli operatori. Ci sono diverse tecniche per rimuovere le bave, dalla sbavatura manuale alla sbavatura termica, effettuata tramite macchinari appositi. La sbavatura è spesso seguita da un rivestimento di conversione per rimuovere ogni traccia di olio, di agenti rilasciati dal pressofuso e di altri contaminanti.
Il processo di rivestimento di conversione consiste nel creare una protezione sul componente in metallo, attraverso la reazione della superficie con un composto chimico. Questo rivestimento è utilizzato per lo più come preparazione e primer per la verniciatura finale, ma può essere utilizzato come finitura definitiva in alcuni casi, soprattutto per i componenti funzionali che una volta assemblati saranno nascosti alla vista: l’uso di un solo trattamento permette di ridurre notevolmente i costi.
Tuttavia, talvolta anche i componenti strettamente funzionali possono richiedere più di un trattamento: quando ci sono delle specifiche funzionali, come la protezione dalla corrosione e la dissipazione del calore, è raccomandato l’uso di una combinazione di rivestimenti di conversione e funzionali per andare incontro alle necessità del cliente.
Per ottenere il miglior risultato ed evitare di scoprire dopo la stampata che un componente non è adatto ad essere sottoposto al trattamento richiesto, è consigliabile consultare un fornitore già in fase di design del prodotto, come vedremo nella prossima parte del post.
I vantaggi della collaborazione per i trattamenti superficiali
Le tecnologie odierne permettono di ottenere prodotti pressofusi con finiture superficiali eccellenti. Per ottenere i migliori risultati e gestire i costi, è essenziale conoscere in anticipo ogni lavorazione che dovrà essere applicata al prodotto. L’applicazione di trattamenti superficiali ai pressofusi implica diverse variabili: la previsione di eventuali problemi e l’identificazione delle possibili soluzioni permette di migliorare il tempo produttivo e di aumentare il risparmio, garantendo allo stesso tempo la qualità richiesta.
Nella produzione industriale, ogni prodotto è definito da precise specifiche e la finitura superficiale dipende da requisiti funzionali o estetici. Anche se l’aspetto di maggior peso nel design del prodotto è sempre lo scopo finale del componente, è necessario tenere a mente che la forma e le geometrie del prodotto possono influenzare la buona riuscita del trattamento superficiale, causando anche difetti visibili.
Per questo motivo la collaborazione tra cliente e fornitore dovrebbe essere costante in ogni fase dello sviluppo del prodotto tramite un’attività di co-design, per individuare le criticità delle forme e ottenere un processo più semplice e definito. Questo permette, ad esempio, di attuare le necessarie modifiche delle superfici, dei bordi e dei punti di montaggio, per ottenere prodotti che richiedono una preparazione superficiale minima prima dell’applicazione del rivestimento finale. Le modifiche del progetto non sono sempre possibili, ma, se attuabili, possono portare a dei miglioramenti consistenti della qualità della finitura superficiale.
Come detto precedentemente, è consigliabile definire i trattamenti post-fusione durante la stesura del progetto. Infatti, le caratteristiche strutturali del prodotto hanno un impatto diretto sull’applicazione di un rivestimento: ad esempio, la presenza di canali e cavità sul componente potrebbe causare sverniciature. Se vuoi saperne di più sull’argomento, puoi leggere questo post.
Una collaborazione tra il fornitore di pressofusi e il cliente può quindi migliorare non solo le lavorazioni post-fusione, ma anche i trattamenti superficiali definitivi, sia di natura funzionale che estetica, come la galvanica o la verniciatura.
Suggerimenti pratici per migliorare i risultati
Come detto nei paragrafi precedenti, ci sono diverse precauzioni che possono aiutare ad ottenere risultati di finitura migliori. Qui sotto elencheremo alcuni accorgimenti che possono essere messi in atto prima dello stampaggio per ottenere vantaggi concreti in termini di design del prodotto e finitura. Questi suggerimenti permettono di semplificare le procedure, tagliando i costi di produzione e finitura.
Linee di divisione
Le linee di divisione sono una delle conseguenze inevitabili della pressofusione: nel punto in cui si congiungono le due metà dello stampo, si formerà una linea di divisione. Una consultazione preventiva con il fornitore sulle necessità estetiche assicura un posizionamento adeguato delle linee divisorie, nascondendo i bordi visibili e di eliminare la necessità di lucidatura post-fusione.
Svasature
Per assicurare l’integrità dei bordi dei fori maschiati, le filettature principali possono essere protette dalla sbavatura o lucidatura tramite svasature o lamature posizionate sui fori del pressofuso prima delle lavorazioni.
Spessore delle Pareti
Quando necessario e applicabile, lo spessore delle pareti può essere aumentato sulle protuberanze per evitare raschiature sulle aree verniciate circostanti.
Nervature di rinforzo
Delle nervature di rinforzo ben progettate permettono di migliorare il riempimento dello stampo e di evitare i segni di risucchio sulle superfici. Protuberanze corte e massicce ottimizzano il flusso del metallo e assicurano l’integrità della configurazione.
Raggio
Utilizzare il massimo raggio possibile per tutti gli angoli interni ed esterni migliora il riempimento delle cavità e rende possibile raggiungere tutta la superficie della parte con strumenti di sbavatura a vibrazione.
Housing
Un buon design degli angoli dell’housing possono assicurare un riempimento complete delle cavità e l’integrità degli angoli.
Superfici texturizzate pressofuse
Durante la costruzione dello stampo, si possono produrre superfici texturizzate su alcune aree selezionate del componente, attraverso una particolare preparazione dello stampo.
Questi sono solo alcuni dei suggerimenti più comuni per migliorare il risultato finale dei processi di finitura superficiale e per ridurre gli sprechi durante la pressofusione, ma un fornitore esparto potrà sicuramente suggerire la soluzione più adatta per ogni prodotto. Dal momento che ci sono diverse variabili da tenere in considerazione a seconda del prodotto, sarebbe impossibile fornire dei suggerimenti universalmente applicabili, dal momento che ogni caso merita particolare attenzione.