Finitura superficiale: come evitare i difetti di cromatura
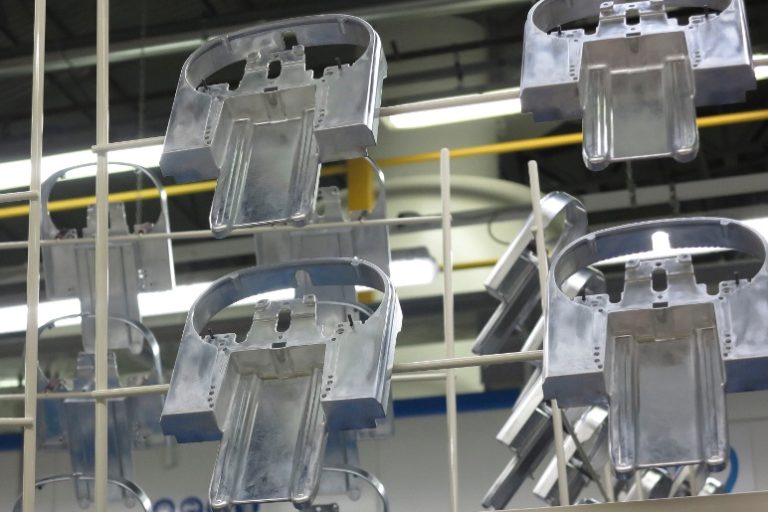
In questo post parleremo dei difetti nella finitura superficiale più comuni quando si lavora con prodotti in lega di zinco. In particolare, parleremo di:
- Blister
- Puntinatura
- Bruciature
- Noduli
- Sfogliature
La finitura superficiale
La finitura superficiale gioca un ruolo cruciale per moltissimi prodotti in lega di zinco: spesso il motivo principale per cui si predilige l’uso della zamak per la creazione di un componente è proprio la grande varietà di finiture e colorazioni che offre, sia attraverso la placcatura sia attraverso la verniciatura. Per questo motivo è importante conoscere e saper prevenire i difetti legati alla qualità superficiale dei pressofusi.
I difetti di finitura superficiale possono essere dovuti a diverse cause, che spaziano dalla qualità del getto a problemi in fase di pre-finitura o finitura. Con pre-finitura si intendono tutte quelle lavorazioni necessarie a preparare il prodotto per i successivi trattamenti di elettrodeposizione o verniciatura, come ad esempio sbavatura, vibratura, pulitura e lucidatura. A seconda della causa scatenante, si possono riscontrare diversi tipi di difetti, ma alcuni sono più comuni di altri.
Tra i difetti più diffusi ci sono i blister e le puntinature: si tratta di difetti che possono essere causati da molteplici fattori, per i quali sarà necessaria un’analisi più approfondita per individuare la causa e procedere alla correzione.
Oltre ai blister e alle puntinature, ci sono altri tre tipi di difetti superficiali facilmente riconoscibili: le bruciature, i noduli e le sfogliature.
I blister
I blister si presentano come delle vesciche in rilievo rispetto alla superficie del pezzo, e le loro dimensioni possono variare a seconda della causa della loro formazione. I blister possono essere infatti causati da difetti nel pressofuso, errori in fase di pre-finitura o errori in fase di elettrodeposizione.
Blister da pressofusione
Questo tipo di blister può essere causato da impurità nella lega, ad esempio dalla presenza di piombo e cadmio, o dalla corrosione intergranulare, ma anche da difetti di stampaggio quali giunzioni fredde e porosità superficiale.
In questi casi i blister si presentano come vesciche rotonde, di grandi dimensioni e dure al tatto. Per una migliore analisi del difetto, sarà necessario tagliare la vescica con una lama affilata: sarà così possibile osservare che, sezionando il blister, si taglierà anche il pressofuso. Tutte queste caratteristiche identificano blister formati a causa di una porosità sub-superficiale sviluppatasi in fase di stampaggio: per questo motivo sarà necessario ridurre la porosità superficiale.
Blister da pre-finitura
Come già detto, i blister non sono sempre causati da difetti nel pressofuso, ma possono formarsi anche a seguito di errori in fase di pre-finitura. Ad esempio, durante la preparazione di un pezzo per l’elettrodeposizione bisogna prestare molta attenzione alla presenza di ossidazioni, corrosioni e altre contaminazioni della superficie del metallo. Infatti, nel caso in cui la superficie non sia perfettamente pulita al momento dell’elettrodeposizione, si assisterà alla formazione di gruppi di blister tondi: tagliando questi blister, il metallo sottostante resterà esposto ed, osservando la sezione al microscopio, sarà ben visibile lo strato di materiale ossidato che ha provocato il problema.
Per evitare queste situazioni, è buona norma evitare ritardi tra colata del getto, pulitura ed elettrodeposizione così da ridurre la probabilità di ossidazioni superficiali. Nel caso in cui non sia possibile evitare un ritardo, ad esempio se ci si rivolge ad un fornitore esterno, una soluzione potrebbe essere di immergere il componente in una soluzione in grado di inibire la corrosione, che andrà poi rimossa prima di procedere alla placcatura. Se, nonostante tutte queste accortezze, si dovessero comunque individuare segni di corrosione sul pezzo, è possibile effettuare una pulitura tramite vibratura meccanica o usando un acido.
Blister causati dall’elettrodeposizione
Un altro tipo di blister facilmente riconoscibile è quello causato da una cattiva adesione tra lo strato di nickel e quello di rame, o tra nickel e cromo. Queste vesciche sono spesso numerose, di forma irregolare e distribuite sull’intera superficie del pezzo, anche distanziate tra loro. A differenza delle precedenti risultano facilmente scalfibili e, una volta rimosse, lasciano scoperto lo strato di rame o di nickel sottostante.
Per evitare la formazione di questo difetto, è necessario assicurarsi che lo strato di rame protettivo sia sufficientemente spesso, che il tempo intercorso tra nickelatura e ramatura sia minimo e che i bagni in cui il componente verrà immerso siano privi di impurità.
La puntinatura
A differenza dei blister, le puntinature sono sempre legate ad errori in fase di pre-finitura o finitura superficiale. Esse si presentano come piccole escrescenze la cui forma e disposizione dipende dalla causa scatenante. Ci sono 4 cause principali per la formazione di puntinature: residui di solvente o schizzi di acido sulla superficie del pezzo, presenza di bolle di idrogeno o formazione di gas nei bagni galvanici.
Nel caso in cui la puntinatura sia dovuta ad un residuo di solvente che ostacola il deposito dello strato rameico si otterranno puntinature disposte in catene o ad anello, mentre se la causa è uno schizzo di materiale corrosivo imprevisto, la disposizione delle puntinature avrà una forma irregolare.
Per risolvere il difetto nel primo caso è possibile cambiare sistema di sgrassaggio, o aggiungere un bagno in liquido freddo tra la fase di sgrassaggio e quella di rivestimento superficiale. La temperatura gioca infatti un ruolo fondamentale in queste fasi: talvolta può essere sufficiente regolare la temperatura dei getti o far trascorrere maggior tempo tra il trattamento in liquido e quello in vapore per evitare la formazione di puntinature che rovinerebbero la finitura superficiale.
Nel caso invece di puntinature a gruppi irregolari, è possibile risolvere il problema controllando la provenienza degli schizzi e correggendola, oppure applicando uno strato di rame più spesso per coprire il difetto.
A volte la puntinatura può essere distribuita casualmente e presentarsi come piccoli crateri dai bordi rialzati: questo avviene quando durante la fase di nickelatura alcune bollicine di idrogeno presenti nel bagno galvanico aderiscono alla superficie del componente.
La presenza di queste bolle può essere dovuta a diversi fattori:
- Insufficiente agitazione del bagno galvanico
- Presenza di tensioattivi insufficiente
- Strato di olio sulla superficie del bagno di nickelatura
- Particelle di polvere che aderiscono alla superficie del componente
Per correggere questo errore, sarà quindi necessario monitorare il livello di agenti bagnanti tensioattivi e l’agitazione del bagno galvanico, oltre a proteggere l’atmosfera circostante per prevenire l’infiltrazione di polveri.
Un ultimo tipo di puntinatura è quello causato dalla presenza di gas e bolle nel bagno galvanico: le bolle si adagiano sulla superficie del componente, creando puntinature tonde e profonde, ravvicinate tra loro e presenti solitamente sull’intera superficie. Per prevenire la formazione di questi difetti, sarà necessario individuare la fonte del gas e controllare l’agitazione dei bagni.
Talvolta è possibile che sia la soluzione stessa ad essere naturalmente ricca di gas, e che lo rilasci nel momento in cui raggiunge una determinata temperatura. In questi casi è possibile rimuovere il gas dalla soluzione portandola ad una temperatura superiore a quella prevista per il processo di galvanizzazione e facendola raffreddare nuovamente prima dell’uso.
Le bruciature
Questo difetto si presenta come una macchia di colore brunito e una sfiammata bruciata sulla finitura superficiale, causate da un picco di densità di corrente o da un bagno contaminato: questa contaminazione può essere causata semplicemente dall’uso della soluzione, poiché particelle di zinco potrebbero staccarsi dal componente e alterare la soluzione.
Per evitarne la formazione è quindi sufficiente cambiare periodicamente il bagno o diluire ulteriormente la soluzione aggiungendo elettroliti.
I noduli
I noduli si presentano come piccole escrescenze che rendono granulosa la superficie del pressofuso: sono la conseguenza della presenza di particolato sul pezzo o nella vasca di nickelatura. Per evitarne la formazione è consigliabile filtrare periodicamente la soluzione e fare attenzione alla pulizia dei pezzi.
Le sfogliature
Le sfogliature sono la conseguenza di una mancanza di adesione dello strato superiore di nickel: si presentano come delle venature numerose ed estese, variabili in forma e dimensione. Sono facilmente scalfibili con un unghia o una lama, e rendono visibile lo strato sottostante.
Le cause sono identificabili in base alla posizione del difetto: se il distacco è formato tra il deposito di Rame e di Nickel, le cause potrebbero essere soluzione contaminata, ritardi di processo oppure attivazione insufficiente. Se invece le sfogliature si sono formate tra lo strato lucido e quello semilucido di nickel, la causa potrebbe essere la passivazione del deposito semilucido. Infine, se la formazione si verifica all’interno del deposito lucido di Nickel, solitamente è dovuta a pulsazioni o interruzioni di corrente durante la deposizione.
In tutti questi casi, per evitare la formazione delle sfogliature sarà quindi necessaria la purificazione delle soluzioni, mentre nell’ultimo caso sarà necessario monitorare il flusso di corrente per evitare interruzioni durante il processo.
Come si è visto, lavorando con la cromatura e l’elettrodeposizione sui prodotti in lega di zinco è possibile incappare in numerosi difetti superficiali, dovuti sia alla qualità del pressofuso che ad errori nei processi di finitura superficiale e cromatura. Alcuni di essi possono tuttavia essere evitati attraverso un monitoraggio costante dei bagni galvanici e delle soluzioni, e un attenta pulizia dei componenti e dell’ambiente di lavoro.