Difetti superficiali di colata nella pressofusione di zinco: marezzature, bolle superficiali e avvallamenti
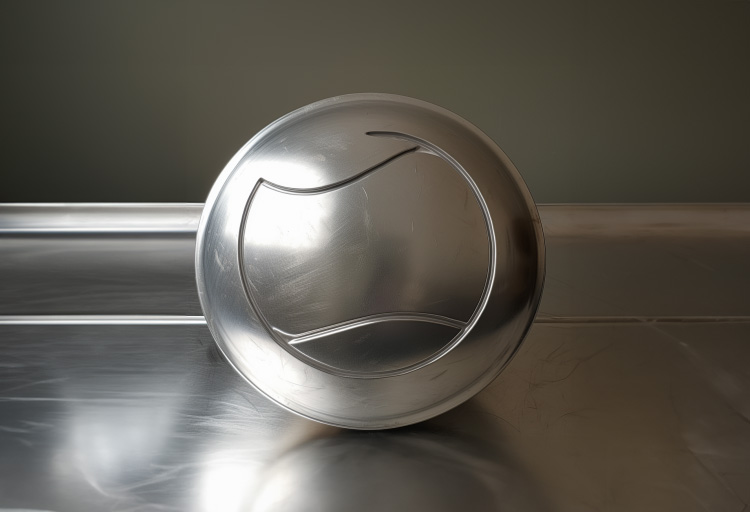
In questo post affronteremo le principali problematiche inerenti ai possibili difetti di colata che potrebbero insorgere nel processo di pressofusione e che comprometterebbero il buon esito di un successivo trattamento superficiale. Questo trattamento, che può essere un trattamento galvanico oppure una verniciatura, può essere effettuato sia per motivi estetici che per motivi funzionali.
In entrambi i casi è importante che la superficie del pressofuso si trovi in condizioni adatte a ricevere i trattamenti previsti, perciò è importante evitare che durante il processo di pressofusione si creino difetti sui prodotti che non permettano al trattamento di verniciatura o al rivestimento galvanico di aderire correttamente al pezzo.
Di seguito analizzeremo i principali difetti di colata che si verificano durante il processo di pressofusione delle leghe di zinco, analizzandone le possibili cause ed i relativi rimedi da adottare in fase produttiva.
Le Marezzature (in inglese “Flow Marks”)
È il difetto più comune del processo di pressofusione ed è generato dal raffreddamento del metallo liquido al contatto con la superficie dello stampo durante la fase di riempimento della cavità. La superficie del pressofuso con marezzature presenta striature e venature che riproducono le linee di flusso del metallo, simili ad una cartina geografica. In fase di iniezione, infatti, in pochi istanti la lega di zinco arriva a contatto con lo stampo e si raffredda bruscamente creando delle sottili lamine sovrapposte che danno luogo al caratteristico motivo tipico delle marezzature sulla superficie del pezzo una volta raffreddato.
Cause delle Marezzature
Le principali cause delle marezzature sono principalmente tre:
- L’eccessivo tempo di riempimento delle cavità dello stampo
- Temperatura stampo e velocità di riempimento troppo basse
- Canali di alimentazione non progettati adeguatamente
In letteratura, come nella pratica quotidiana in fonderia, è
ormai chiaro che è quasi impossibile ottenere un pressofuso completamente esente da questo difetto: è perciò importante saper valutare e definire il grado di accettabilità. Un eccessivo grado di marezzatura può causare, come precedentemente anticipato, infatti difetti in fase di verniciatura o di trattamento galvanico a causa delle irregolarità della superficie. Le micro-fessure superficiali della marezzatura possono infatti intrappolare gas o aria che vengono poi rilasciati nelle varie fasi dei processi di verniciatura o galvanici generando difetti estetici quali micro bolle, puntinature, micro crateri, non tollerati sia a livello estetico che a livello funzionale.
Soluzioni: come evitare le Marezzature
L’eliminazione o quanto meno la riduzione del problema delle marezzature si ottiene attraverso la corretta regolazione dei principali parametri di stampaggio: quali la velocità di riempimento e la temperatura della superficie dello stampo. In questo modo è possibile velocizzare il tempo di riempimento, riducendolo a pochi millisecondi, per evitare il formarsi delle lamine di materiale freddo sulla superficie del pressofuso.
Questo tipo di difetto di colata è quindi prevedibile già in fase di progettazione dello stampo: infatti una corretta analisi tramite il programma di simulazione consente la progettazione dei punti di iniezione e delle sagome dei canali di alimentazione ottimali in modo da ottenere portate e velocità di riempimento adatte ad evitare così il problema delle marezzature nel processo di pressofusione di zinco.
Le Bolle superficiali (in inglese detto “Blistering”)
Le bolle superficiali sono un difetto di porosità dovuto all’intrappolamento di gas all’interno di una regione sub-superficiale del pezzo. Questo difetto di colata è caratterizzato da una piccola area superficiale che si deforma quando la pressione interna della porosità dovuta al gas sotto la superficie è elevata tanto da deformare in modo plastico il sottile strato metallico che lo ricopre. Generalmente le dimensioni delle bolle possono variare da 100 µm a diversi mm.
Cause delle Bolle superficiali
La deformazione del metallo avviene facilmente a temperature relativamente elevate, quando i getti vengono espulsi dallo stampo o durante successivi trattamenti termici. Questo tipo di difetto è principalmente imputabile al riempimento turbolento dello stampo e del conseguente intrappolamento d’aria presente nei canali di alimentazione e nelle cavità dello stampo. Si tratta di un difetto ben noto ai verniciatori poiché, nel processo di verniciatura a polvere, la fase finale prevede un passaggio in forno a temperature di circa 200°C e, a questa temperatura, l’eventuale gas o aria intrappolata nei pressofusi si espande e in caso di prodotti a spessori sottili oppure in caso di inclusioni di aria prossime alla superficie genera le bolle superficiali.
Soluzioni: come evitare le Bolle superficiali
Vediamo di seguito quali sono i diversi accorgimenti per evitare l’insorgenza di questo difetto:
Analisi
La prima attività da svolgere è un’approfondita analisi dei dati forniti dal programma di simulazione di riempimento. Con tale programma vi è infatti la possibilità di individuare le zone del prodotto a maggior rischio di intrappolamento d’aria. A seguito di queste informazioni è possibile dimensionare le sezioni di iniezioni ed i canali di alimentazione in modo da evitare gli intrappolamenti. Le macchine moderne protagoniste (Pre-filling, FDS) del processo di pressofusione di zinco sono dotate di sistemi che riducono l’immissione di aria durante la fase di riempimento, riducendo ovviamente il fenomeno, ma non eliminandolo completamente.
Stampaggio sotto vuoto
La soluzione più importante ed efficiente è l’impiego del sistema di stampaggio sotto vuoto: estraendo cioè l’aria dalle cavità dello stampo prima che il metallo le raggiunga. Questo sistema garantisce una drastica riduzione degli scarti dovuti alla presenza di bolle superficiali, sia in fase di stampaggio che in fase di trattamenti superficiali successivi.
Gli Avvallamenti (in inglese “Sink”)
L’avvallamento è una depressione superficiale che si crea in fase di raffreddamento dei pressofusi dovuta alla presenza di una porosità da ritiro sotto la superficie. Questo difetto di colata appare come una depressione concava, anche di diversi mm, solitamente in corrispondenza di alti spessori o di forti cambi di spessore del prodotto ed è frequentemente associato a nervature.
Causa del fenomeno dell’avvallamento
È un fenomeno che si verifica quando, durante la solidificazione del getto, un punto caldo si trova vicino alla superficie dello stampo: lo strato di “pelle”: formatosi in conseguenza al raffreddamento della zama al contatto con lo stampo, non è in grado di sostenere le sollecitazioni derivanti dalla contrazione della regione sottostante in solidificazione (ritiro) e quindi si deforma plasticamente.
Gli effetti di questo difetto si traducono in inestetismi del prodotto finito.
Soluzioni al difetto dell’avvallamento
Il rimedio principale consisterebbe nella corretta progettazione dei componenti, facendo cioè in modo che non vi siano forti cambi di spessore oppure zone di prodotto a spessore eccessivo. Purtroppo non è sempre possibile eseguire la sagoma ideale alle esigenze funzionali del prodotto,
È perciò importante, in fase di progetto di un nuovo prodotto, che vi sia una stretta collaborazione tra il progettista ed il pressocolatore allo scopo di individuare le sagome più corrette, in modo da ridurre gli avvallamenti, nel rispetto delle funzionalità del prodotto.
Per evitare gli avvallamenti durante il processo produttivo è inoltre possibile agire sulla pressione e sulla velocità del metallo fuso in fase di iniezione. Ancora più importante infine è la gestione del bilancio termico dello stampo, realizzando adeguati sistemi di raffreddamento atti ad evitare la formazione di punti caldi. Anche in questo caso l’analisi della simulazione di raffreddamento ci viene in aiuto nell’individuare le zone del pressofuso con i tempi di raffreddamento più alti e ci consente di realizzare il circuito di raffreddamento più efficiente, adatto ad evitare il difetto degli avvallamenti.
In conclusione
Come accennato nell’incipit di questo post abbiamo trattato le principali problematiche inerenti i possibili difetti di colata nel processo di pressofusione di zinco. Come precedentemente esposto tutte le problematiche si possono prevedere e risolvere oppure definirne un grado di accettabilità: l’importante è sapere come riconoscerle e prevenirle. Esistono altre problematiche oltre a marezzature, bolle superficiali e avvallamenti nella pressofusione di zinco. Problematiche che è possibile discutere in maniera approfondita: cerca queste tematiche nel nostro blog.