L’importanza dell’automazione per migliorare il processo produttivo
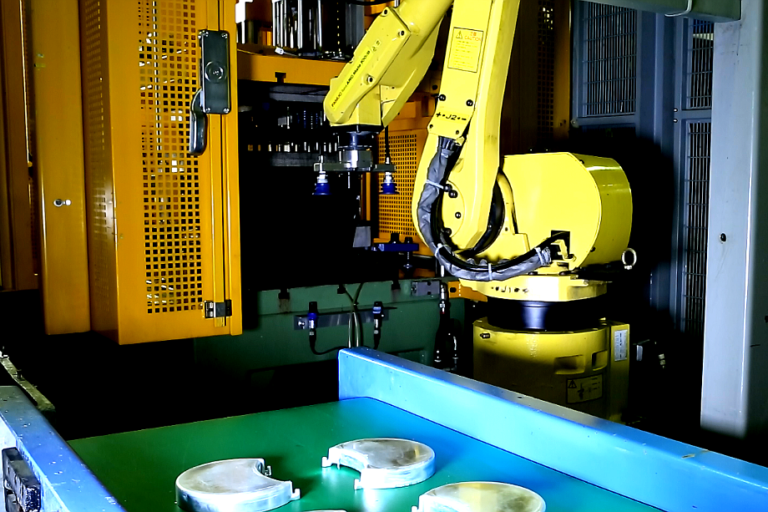
In questo post esamineremo un case study relativo a un progetto di riduzione delle operazioni manuali attraverso l’introduzione di automazione, che ha apportato benefici all’intero processo produttivo.
Con il termine automazione si definisce l’introduzione, in un’azienda manifatturiera, di strumenti e processi atti a ridurre e/o eliminare operazioni meccaniche svolte manualmente da operatori. Infatti, il principale beneficio che l’automazione apporta è la riduzione del carico di lavoro degli operatori, che di conseguenza genera ulteriori vantaggi quali lead time ridotto, abbattimento dei costi e raggiungimento degli standard qualitativi richiesti dai clienti. L’automazione può quindi contribuire al miglioramento del processo produttivo, ottimizzando accuratezza, precisione, produttività e uniformità degli output.
CASE STUDY
In Bruschi siamo sempre alla ricerca di soluzioni innovative da adottare per ottimizzare il processo produttivo. Allo scopo di raggiungere questo obiettivo, il reparto produzione ha sviluppato un progetto di riduzione del carico di lavoro dell’operatore attraverso l’introduzione dell’automazione. Questo progetto riguarda due particolari componenti prodotti per un cliente del settore dei piccoli elettrodomestici e ha ottenuto eccellenti risultati in termini di riduzione delle attività manuali e aumento della produttività.
Per definire i due prodotti da efficientare tra quelli disponibili, è stata effettuata un’analisi con il supporto del diagramma di Pareto. Dall’analisi sono emersi i seguenti risultati:
• Il 20% del volume prodotto è realizzato dal 0,05% degli articoli
• Il 60% del volume prodotto è realizzato dal 17% degli articoli
• Il 20% del volume prodotto è realizzato dall’82,95% degli articoli
I risultati evidenziano che lo 0,05% degli articoli genera il 20% del volume prodotto in Bruschi: questi componenti vengono perciò definiti prodotti runner. La presenza di un ridotto numero di articoli che realizza una percentuale così consistente del volume totale consente l’introduzione in produzione di un’automazione dedicata, senza che quest’ultima causi una riduzione della flessibilità produttiva.
Definizione delle fasi
Dopo aver selezionato i componenti è possibile definire le diverse fasi del progetto. La gestione del processo iterativo di miglioramento è infatti scomposta in quattro fasi, in riferimento al ciclo PDCA o ciclo Deming:
• Fase 1 – PLAN
Definizione del problema, individuazione delle cause ed ipotesi azioni correttive per
raggiungere gli obiettivi previsti.
• Fase 2 – DO
Implementazione azioni correttive previste al punto 1.
• Fase 3 – CHECK
Raccolta dati e controllo. Confronto tra risultati attesi e risultati riscontrati.
• Fase 4 – ACT
Implementazione delle azioni correttive emerse dall’analisi dati prevista al punto 3.
Le quattro fasi del ciclo PDCA sono state pianificate utilizzando il seguente diagramma di Gantt:
Fase 1 – PLAN
La prima fase ha inizio con la definizione del problema: una condizione di disallineamento tra capacità produttiva e richiesta del cliente, con ipotesi di stampaggio dei due componenti sulla stessa pressa, causato dallo stato di saturazione dell’impianto produttivo. Di conseguenza, il problema non può essere risolto stampando i due componenti su due differenti macchine per la pressofusione: risulta infatti necessario ottimizzare il processo di produzione dei componenti.
L’individuazione della causa radice passa attraverso lo studio e la definizione della durata media delle singole attività, manuali dell’operatore e meccaniche della pressa:
• Stampaggio – operazione automatica gestita dalla pressa
• Prelievo stampata e deposito su tavolo – operazione automatica gestita dal robot antropomorfo
• Separazione masse di scarico e rilavorazione – operazioni manuali gestite dall’operatore
• Attività ausiliarie – operazioni manuali gestite dall’operatore
Una volta calcolati i tempi medi di ogni singola attività, il miglioramento si focalizza su quelle che possono apportare maggiori benefici, ovvero quelle che impiegano l’operatore per un periodo di tempo maggiore. Le attività manuali selezionate sono rilavorazione, separazione grezzo-scarto, e alimentazione pressa: queste impegnano l’operatore per il 97% del suo tempo.
Il secondo step concerne la classificazione delle operazioni in funzione del valore aggiunto che apportano al cliente:
• VA = 0 % – Attività necessaria a valore aggiunto: riconosciuta, quindi pagata dal cliente
• NVA = 3 % – Attività non necessaria e non a valore aggiunto: non riconosciuta, quindi non pagata dal cliente
• NNVA = 97% – Attività necessaria e non a valore aggiunto: non riconosciuta, quindi non pagata dal cliente
Le prime attività da prendere in considerazione e da eliminare sono le attività NVA, poiché si tratta di attività che non apportano valore e il cliente non le conosce. In secondo luogo le attività da efficientare sono quelle NNVA, poiché le VA possono essere migliorate, ma solamente con un margine ridotto.
Fase 2 – DO
Una volta individuate le operazioni da efficientare è necessario effettuare un’analisi costi-benefici al fine di individuare la soluzione migliore tra esternalizzazione o efficientamento interno attraverso automazione. Entrambe le soluzioni sono state implementate:
• Esternalizzazione pari al 50% delle attività manuali
• Riduzione pari al 45% delle attività manuali, attraverso l’introduzione di automazione che effettua la separazione automatica dei pezzi dal canale di colata e la rifusione automatica del canale di colata
Fase 3 – CHECK
La terza fase del progetto ha riguardato raccolta e controllo dati, con confronto tra risultati attesi e risultati ottenuti. Il periodo di osservazione a seguito delle azioni correttive è stato di 240 ore lavorative. Per valutare l’efficacia dell’intervento sono stati presi in considerazione tre KPI (Key Performace Indicators) numerici:
1. OEE – Overall Equipment Effectiveness
2. Durata media attività manuali
3. Tonnellate di zama rifuse a bordo macchina
I dati emersi dal confronto degli indicatori prima e dopo l’intervento hanno riportato un +33% di OEE e un -95% delle attività svolte manualmente, con una completa rifusione del materiale di scarto.
Fase 4 – ACT
Durante la fase 4 non è stato effettuato alcun intervento poiché dall’analisi dei KPI non sono emerse anomalie.
BENEFICI CONSEGUITI
Il progetto ha apportato molteplici benefici, sia diretti che indiretti.
Benefici diretti:
• +33% OEE
• -95% attività manuali
• Completa rifusione scarto bordo macchina
Benefici indiretti:
• Aumento della soddisfazione del cliente. Lead time rispettati e ridotti grazie all’aumento di capacità produttiva, al miglioramento qualitativo superficiale del pezzo e alla stabilizzazione dei processi di separazione canale-pezzo e di rilavorazione
• Risparmio energetico associato alla fusione immediata della materia prima
• Riduzione degli sprechi di movimentazione associati all’annullamento di spostamento dello scarto
Da questo case study risulta evidente l’importanza dell’automazione in un sistema produttivo efficiente e avanzato: attraverso l’introduzione di sistemi automatici è stato infatti possibile soddisfare gli standard quantitativi e qualitativi richiesti dal cliente, rispettando al contempo le deadline stabilite.
Se desideri approfondire le tue conoscenze sui metodi di ottimizzazione del processo produttivo, ecco ulteriori post sull’argomento:
• Come migliorare il processo produttivo per l’industria della pressofusione
• Ottimizzazione del processo di pressofusione: sistema di alimentazione