Simulazione per pressofusione: studio per la riduzione degli scarti
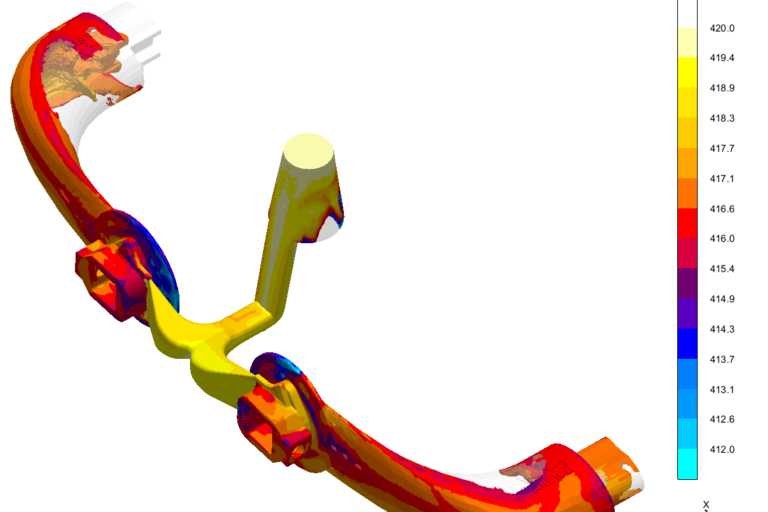
In questa serie di post, spiegheremo l’importanza della simulazione per pressofusione attraverso esempi concreti in cui la simulazione ha avuto un ruolo fondamentale.
Nel post di oggi, dopo una breve introduzione, analizzeremo un caso del settore delle automazioni riguardante la formazione di bolle e di problemi di intrappolamenti di aria che sono stati risolti grazie all’uso di un software di simulazione.
Durante il processo di pressofusione delle leghe di zinco, l’elemento che più influisce sul risultato finale è il canale dell’alimentazione, che porta la lega nello stampo. Una corretta alimentazione dello stampo ha un’importanza cruciale per la qualità, la forza e la superficie del prodotto, e può anche allungare la vita dello stampo.
Una simulazione dell’alimentazione, del riempimento e della fase di solidificazione offre un vero vantaggio: aiuta infatti a prevedere i possibili difetti causati da flussi liquidi non uniformi, da gradienti di temperatura troppo elevati, aumenti della velocità locale e altri problemi. Con i software di simulazione è possibile ottimizzare l’intera produzione, con effetti positivi sulla durata della vita dello stampo e sul prodotto finale, in termini di estetica e efficienza. Queste simulazioni si svolgono utilizzando software specifici, come Magmasoft.
Magmasoft è un pacchetto software innovativo sviluppato appositamente per la simulazione per pressofusione. Permette di simulare il riempimento dello stampo e la solidificazione del pressofuso, calcolando il flusso delle leghe, la loro temperatura e la presenza di gas o porosità nel prodotto finito.
Grazie a queste simulazioni, è possibile identificare la configurazione migliore per gli alimentatori e per ottenere i migliori risultati per precisione e affidabilità, riducendo i rischi al minimo e risparmiando tempo e risorse.
In questa serie, analizzeremo dei casi in cui l’analisi tramite simulazione ha contribuito a migliorare la produzione corrente e ad evitare errori di progettazione che avrebbero influito il prodotto finto, creando sprechi di materiale, tempo e risorse.
Nel dettaglio, presenteremo 5 diversi casi in cui l’uso di un software di simulazione ha influenzato le decisioni nella scelta delle tecniche per la produzione dei pressofusi. Ecco una lista degli argomenti che andremo a trattare in ogni post:
- Riduzione degli scarti
- Qualità estetiche
- Caratteristiche meccaniche
- Manutenzione e ciclo vitale dello stampo
- Ottimizzazione dei parametri
Ora presenteremo il primo caso, relativo alla riduzione degli scarti per un prodotto utilizzato nel settore delle automazioni industriali e della gestione energetica.
RIDUZIONE DEGLI SCARTI: UN CASO DAL SETTORE DELL’AUTOMAZIONE
Questo studio riguarda un supporto per un interruttore di emergenza. Data la sua funzione, il prodotto è visibile ma non necessità di alte qualità estetiche. Tuttavia, il prodotto veniva sottoposto a verniciatura: questo processo portava alla luce dei difetti superficiali.
Lo stampo di questo prodotto è stato utilizzato per diversi anni, generando sempre una percentuale di scarti del 5% causata dalla formazione di bolle durante la verniciatura. L’origine di questo fenomeno è la presenza di aria nella lega, che viene spinta verso l’esterno dalle alte temperature raggiunte durante il processo di verniciatura e rimane intrappolata tra la superficie del pressofuso e lo strato di vernice.
Obiettivi e fasi della simulazione
In questo studio di simulazione ci si è concentrati sull’evitare bolle nelle fasi di post-produzione. L’obiettivo della simulazione era di ridurre la quantità di scarti causati dagli intrappolamenti di aria. Abbiamo esaminato il comportamento del flusso durante le fasi di riempimento per accertare le cause di questo fenomeno. In seguito, abbiamo studiato metodi di alimentazione alternativi.
Risultati della analisi
L’analisi mostra aree di reflusso e incapsulamento dell’aria in prossimità dei bordi, dove erano state identificate le bolle. Questa turbolenza è causata dalla velocità del flusso e dalle caratteristiche geometriche del componente.
Nell’immagine seguente, potete vedere il risultato di un’analisi numerica della configurazione attuale dello stampo:
Una volta che la causa del problema è stata identificata, è stato possibile cercare una soluzione che potesse ridurre la velocità del flusso.
SOLUZIONE
La soluzione rappresentata nell’immagine prevede un sistema di alimentazione alternativo, dove il canale di colata è ruotato di 45° attorno all’asse del prodotto.
I risultati della modifica sono illustrati di seguito.
Paragone tra le due configurazioni:
Attraverso l’uso di una simulazione, l’area di reflusso è stata completamente eliminata e il flusso di riempimento risulta più uniforme.
Dopo la simulazione, lo stampo è stato modificato e i risultati hanno confermato la validità dello studio: la quantità di prodotti rifiutati a causa delle bolle è stata ridotta quasi del 95%.
Riassumendo, grazie all’uso della simulazione per pressofusione è stato possibile identificare chiaramente le aree problematiche in cui si formavano gli intrappolamenti di aria. La rotazione del condotto di alimentazione ha permesso di regolare la velocità del flusso senza modificare la forma del componente, prevenendo il reflusso nelle aree identificate precedentemente. Dopo le modifiche al sistema di alimentazione, la percentuale di scarti causata dalle bolle è stata ridotta significativamente.
Questo è solo uno dei tanti esempi in cui l’uso di una simulazione per pressofusione può aiutare a migliorare la produzione.